What to Know About Controlling Dust During Remodeling
Dust is everywhere, all the time. But during a remodeling project, it’s particularly abundant — and potentially hazardous. All sorts of nasty stuff gets kicked up while demolishing walls, taking apart cabinets and removing tile. And it’s not for the faint of heart. Waste from bugs, mice, spiders and bats; silica from drywall; lead particles from old paint — if it was in your walls or subfloor, it’s probably going to be in your home (and lungs). Unless, that is, your remodeling crew has a solid strategy for containing and removing the dust from your home.
“Construction can produce inhalable respirable particles that are regulated pollutants; they’re unhealthful, so it’s entirely appropriate to do some kind of mitigation when doing construction activities,” says Brett Singer, an indoor air quality scientist at Lawrence Berkeley National Laboratory. There are several strategies for doing this, and if dust is a concern to you, it’s important to have a conversation with your contractor when taking bids to determine how they plan to contain construction particles. Here are some things to think about before having that talk.
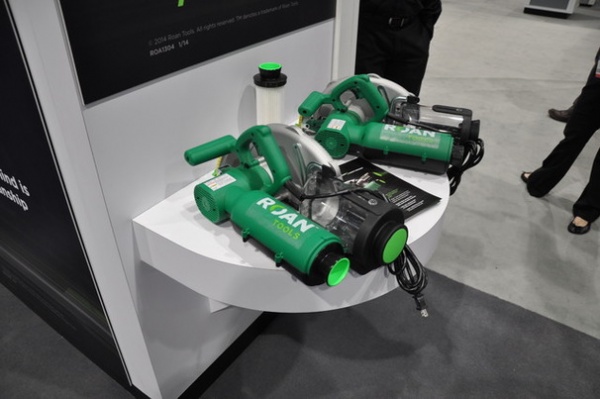
1. Power tools with dust extractors. Several companies, including Festool and Roan Tools (shown here) make power tools that have vacuum extractors to suck up dust at the point of contact. So a saw or sander can collect sawdust as it’s cutting, a tile cutter can capture tile debris, and so on. These tools can remove nearly 90 percent of dust at the point of generation.
But power tools are used during only about 10 to 20 percent of demolition work, says Brian Paich of BuildClean, a company that makes high-powered dust filters that we will discuss later. So even if these tools are used, you’re still left with plenty of dust in the air during activities like knocking down drywall. “You can’t attach a vacuum on a sledgehammer,” Paich says.
Not all contractors have these tools on hand, so it’s something you can ask about during the interview process. The tools can run upward of $6,000 to $7,000 for a set, and contractors who do have them often have higher overhead in their bids as a result. You may want to consider whether the additional cost is worth it to you and your family.
No matter what, dust-generating tasks such as sawing should take place outside the home whenever possible.
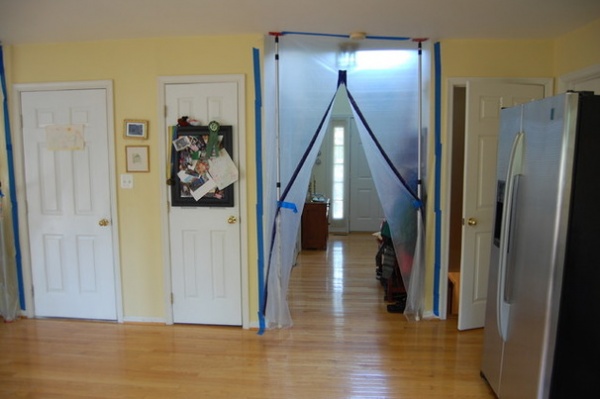
2. Dust barriers. At a minimum, contractors should apply plastic over the entry points of a room under construction. These barriers, commonly referred to as zipwalls, contain dust within a particular space and have a zippered entry.
Of course, entering and exiting through these barriers creates a situation where dust has the potential to escape into the home.
David Casillas, a general contractor for Rockin’ Fine Finish, uses power tools with dust extractors, dust barriers and air scrubbers to control dust during construction projects.
He recommends talking with your contractor about how the debris will leave the room. For example, if it’s a kitchen remodel you’re doing, how will the demolished cabinets, countertops and drywall be removed? Will they travel through your home and out the front door? Or can materials be sent out a window or through the garage to help keep dust from reaching the rest of your home?
Also, Casillas says, it should go without saying that the crew and subcontractors won’t venture into areas of the home that aren’t being worked on. “Everyone should stay within the working area and not move dust from room to room,” he says.
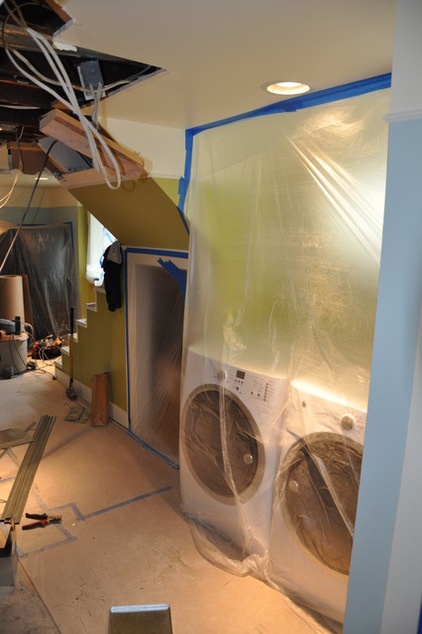
Outside the area under construction, say in a doorway, contractors should place sticky mats that pull dust off shoes. Floor paper should line the walkway from the area under construction to the exit door, capturing additional dust.
Also, make sure your crew is doing adequate cleanup at the end of the workday. Vacuums and sponge mops should be used to gather any dust that’s settled.
As for HVAC systems, any vents should be blocked off with plastic. If there’s a return vent in the room in which work is occurring, that’s a bigger issue. These usually cannot be blocked off because they keep the system running, and damage can occur if air isn’t being returned while the system is on.
For a home in, say, Arizona that needs to have the air conditioning running during the summer, this could pose a problem. Casillas says these systems can be strategically blocked off for an hour or two while the dusty work is being done. That’s about how long it takes, he says, for a home to start heating up. Or he might move that portion of work to a weekend or morning when the homeowners aren’t there and the system can be turned off. Sometimes a shutoff is simply unavoidable, and whoever is in the house will have to deal with being uncomfortable.
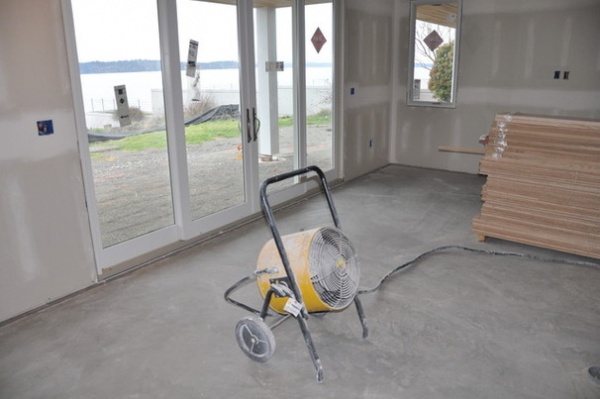
Contractors sometimes place a fan near a window to blow the air in a room under construction outside to create negative air pressure, so that when the plastic barrier is opened, the dusty air doesn’t rush into the rest of the home.
The problem here is that you run the risk of blasting tainted air outside — into the atmosphere or all over your neighbor’s house. If you have a home built before 1972, you could potentially be blowing toxic lead dust outside. That’s why the EPA’s Lead Renovation, Repair and Painting Rule dictates that lead dust be contained. Contractors working on homes built prior to 1972 can face huge fines if they blow such dust out a window.
Homes built after 1972 aren’t off the hook, either. Crystalline silica is found in sand, stone, rock, concrete, brick block and mortar and can be released during construction work. The Occupational Safety and Health Administration cautions that “these types of exposures can lead to the development of disabling and sometimes fatal lung diseases, including silicosis and lung cancer,” according to information on the OSHA website.
“Because of the potential risks, and to just be a good neighbor, the rule of thumb in the industry is to never vent unfiltered air out of a structure under construction,” BuildClean’s Paich says.
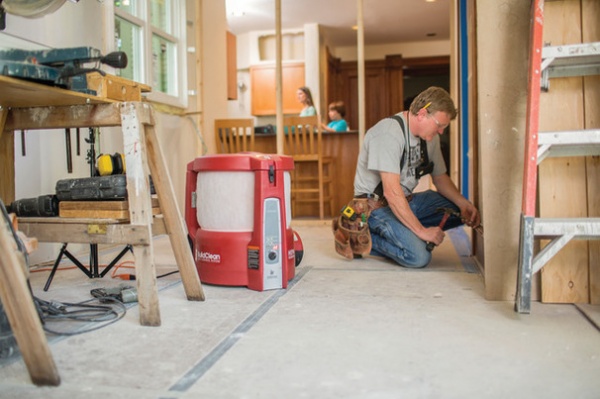
3. Air scrubbers. You can’t eliminate dust generated during construction, but you can capture it when it’s airborne before it travels into your home. That’s where air scrubbers come in. These smallish portable machines pull in dusty air, filter it and then send out clean air, which you can vent out a window.
The added cost to have filters on your project depends on the scope and square footage involved. The filters are pricey and usually must be changed out every 20 minutes, putting the burden on contractors to remember to do it. Rental units, from companies such as Sunbelt, usually run $150 to $200 per week, Paich says. Dri-Eaz is another company that makes similar air scrubbers, but theirs tend to focus mainly on mold and fire remediation.
The BuildClean, shown here, which the company doesn’t rent but sells to contractors for $980 a unit, has six times more filter area than its counterparts and offers 360 degrees of dust-catching. The fan RPMs increase as the filter gets loaded so there’s no slowdown. And the machine alerts workers when it’s time to change or shake out the filter.
The BuildClean filter can last for two days while working with drywall or sanding, about four hours while removing horsehair plaster and about an hour while doing heavy concrete demo work. During an average job, the filter lasts a day, Paich says.
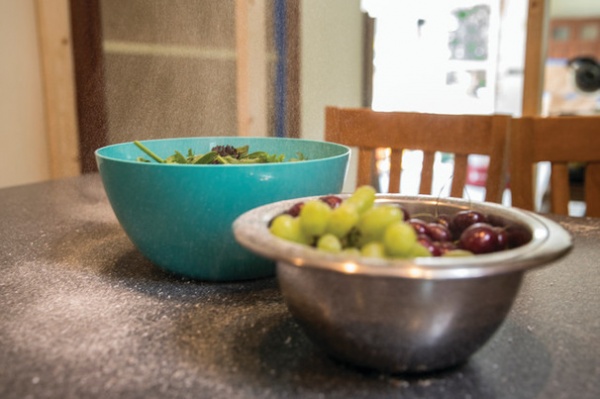
The machine runs at 600 cubic feet per minute. That’s six air exchanges per 6,000 cubic feet per hour. For a typical kitchen, that means the air is being completely refreshed every 10 minutes.
Paich says a cubic foot of air in a typical office environment contains 30,000 to 50,000 particles of dust larger than 0.5 microns. During a remodel, that number can increase to 700,000 to 1 million particles per cubic foot. You still can’t see that dust in the air, but when it settles, that’s when you look at your black lacquer piano and realize what you’ve been inhaling. “If you have a child with asthma or you are an elderly couple aging in place and you’re remodeling your house, all that particulate in the air could be really dangerous,” Paich says.
Running a BuildClean, Paich says, can get 860,000 particles per cubic foot in the air to less than 100,000 particles per cubic foot in 10 minutes. In half an hour, the air will be back to the normal 30,000 particles. In one hour, after six air exchanges, it’s at 16,000 particles per cubic foot.
But Singer, the indoor air quality scientist at Lawrence Berkeley National Laboratory, says HEPA filters might be overkill, since they’re designed to pull out smaller particles from the air not associated with construction dust, which tends to consist of larger particles. These particles won’t get into your lungs, he says, but could get caught in your respiratory tract. Singer says MERV 8 to 11 filters should get the job done, and they’re less expensive than HEPAs.
Either way, Singer says, a collective approach of using tools with vacuums, barriers and filtration should be effective at mediating potentially harmful dust.
More: What You Need to Know About Dust and How to Fight It