Houzz Tour: Childhood Memories Shape a Lakeside Cottage
Mike Mulvagh has a deep history with his family’s summer lakeside property in Quebec. In 1948 his grandfather built a cottage on the land, and Mulvagh spent nearly every summer there from the time he was born. The one-story cottage got handed down through his family over the decades, and by the time Mulvagh inherited it, carpenter ants had left it uninhabitable. He had hoped he’d be able to renovate the home, but he soon realized nothing was salvageable.
He found architect Paul Kariouk through an Internet search, and the two connected immediately. Since Kariouk was working with a relatively blank slate, he produced several design iterations, including a U-shaped design with a courtyard and a two-story version. But though Mulvagh loved the designs, he found himself reluctant to lose the original feel of the home. In the end he let his emotions win. “I was anxious about tearing down the family history and all the memories we had there, so we decided to keep it exactly on the same footprint,” says Mulvagh, who lives in Manhattan with his partner, Chip Crosby. “We decided to default back to the emotional side.”
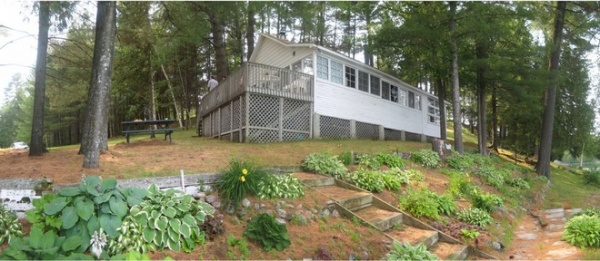
Houzz at a Glance
Location: Ladysmith, Quebec
Who lives here: This is a vacation home for Mike Mulvagh, head of corporate communications for Moody’s, and Chip Crosby, a child psychologist.
Size: 1,000 square feet (93 square meters); 2 bedrooms, 1 bathroom
BEFORE: The original cottage didn’t have indoor plumbing, so an outhouse was used until the 1960s or 1970s, when the home got its only previous update — two bedrooms and a bathroom.
The home was also poorly insulated, making it difficult to visit during chillier months. “It was often cold when it shouldn’t have been,” Mulvagh says. “It wasn’t really that great to be there in the spring or fall.”
Because Quebec law states that any dwelling within 100 feet of a shoreline can’t be changed, Mulvagh and Kariouk had to stay within the same footprint if they kept the cottage in the same place. They could have moved farther away from the water and built anything they wanted, but Mulvagh says it just didn’t seem practical. Plus, the view of the lake was what the home was all about, and Mulvagh had some sentimental attachment to the cottage’s location.
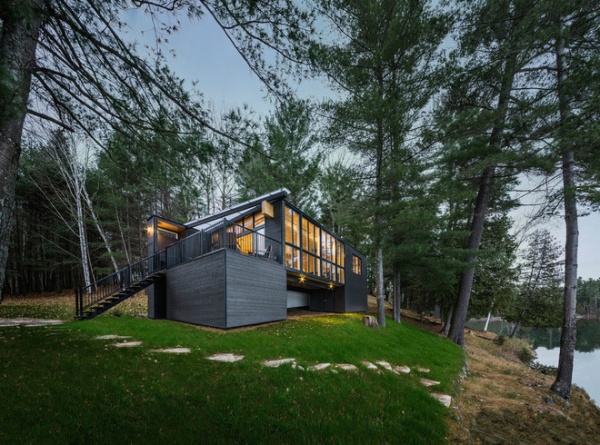
Photos by Photolux Commercial Studio
AFTER: The old cottage came down and was replaced with a new structure. This isn’t Mulvagh’s grandfather’s cottage: While the new home is in the same footprint, it has 10 times more windows, and the materials are entirely modern. Mulvagh and Crosby chose a construction method that used cedar laminated timber (CLT).
Six-inch wood panels were designed and built offsite, then delivered to the property. The home was assembled in a couple of days by Gilles Langlois of GPL Construction. “Ninety percent of the home was built offsite and assembled onsite, including the kitchen cabinets,” architect Kariouk says. The electrical, plumbing and roof membrane were all done onsite.
While the method cost the same as it would have had they built a stick-frame construction, CLTs make for a more durable, longer-lasting home. “We wanted to build a summer place that would last and that would suit us into older age and that wasn’t going to break the bank,” Mulvagh says.
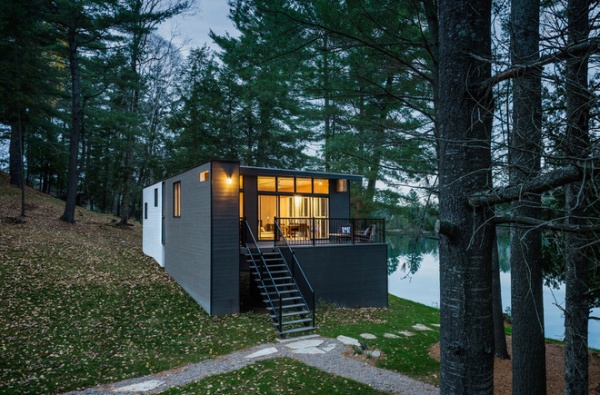
The layout stayed generally the same. For example, you still enter by taking the stairs up to the porch.
The sloping land meant there was 5 to 12 feet of space beneath the home that wasn’t being used. Kariouk brought the siding down to the ground to create enclosed storage for canoes and outdoor furniture.
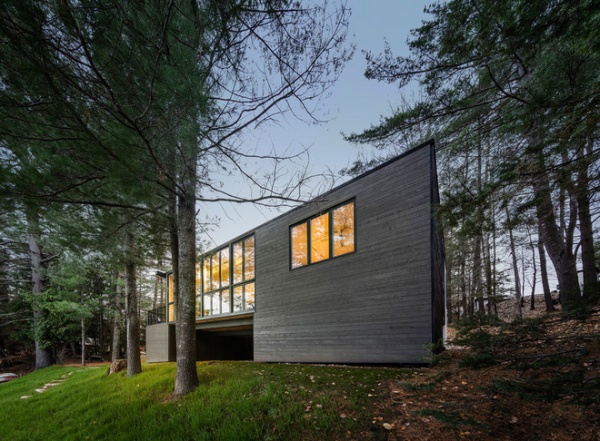
Pine siding covers the exterior of the home.
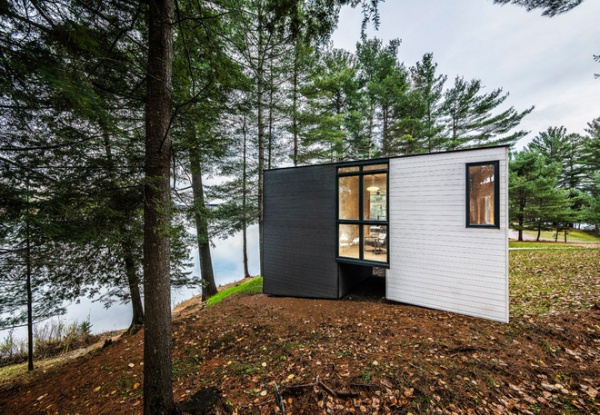
Dark brown and off-white portions delineate the separate spaces. To the left is the master bedroom; to the right, the guest room. A reading nook is between the two.
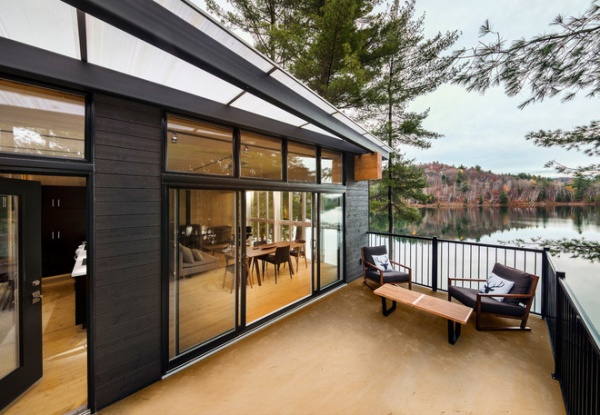
Even the deck remained the same size as the original. CLT treated with epoxy paint forms the floor of the porch. Here you get a glimpse of the view to the private lake.
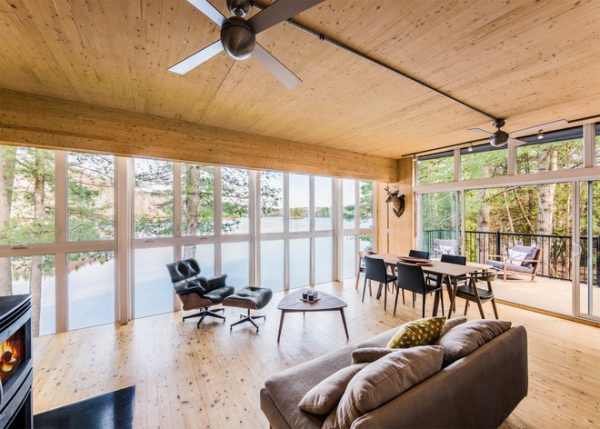
Mulvagh says they wanted to lean toward a more Scandinavian look. Keeping the light-blonde spruce CLT panels raw helped give the interior of the home that vibe.
The woodstove on the left provides heat, while the thick CLT panels keep that heat contained. “It’s a modern version of a log cabin,” Kariouk says. A plate of quarter-inch steel creates a noncombustible surface in front of the fireplace.
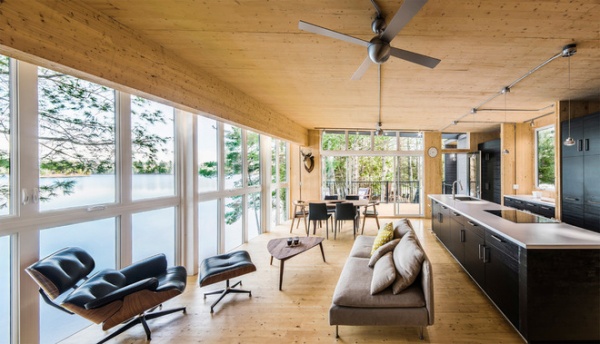
A large glulam beam on the upper left extends across the living space to hold up the roof and achieve an unobstructed wall of windows.
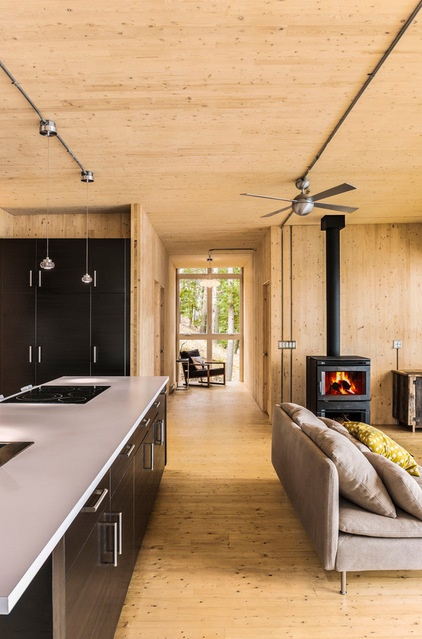
A hallway leads to the two bedrooms and the reading nook. Mulvagh and Crosby are considering a rock wall treatment for behind the woodstove.
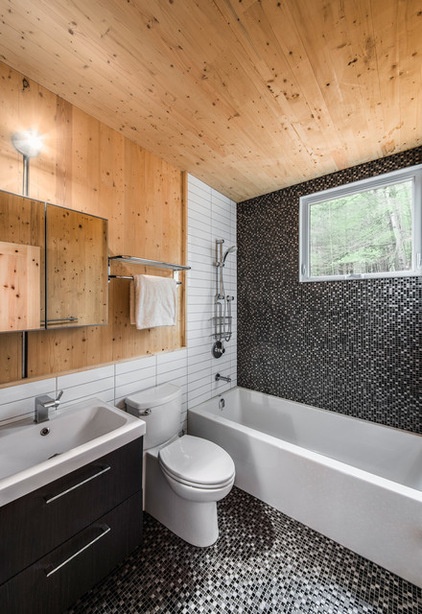
Mosaic tile in the bathroom offers a slight break from all the wood in the cottage.
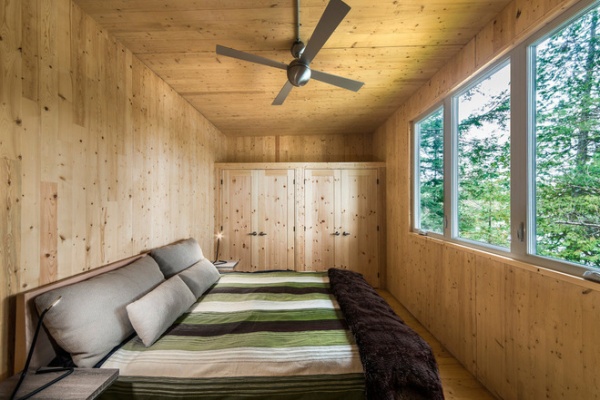
In the master bedroom, conventional pine cabinets were matched to look like the CLT.
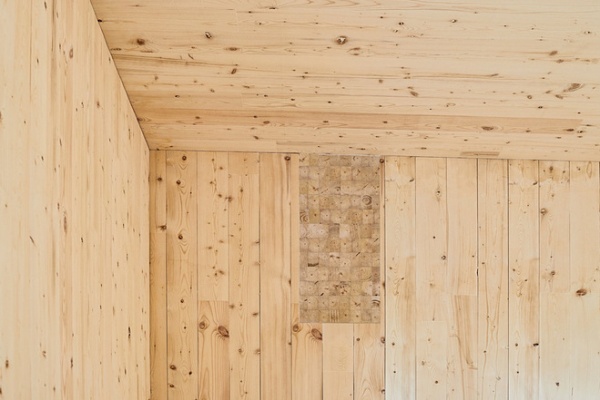
Also in the bedroom, you can see the end of the structural glulam beam that runs across the living room. Kariouk says he could have covered it with a piece of wood, but he wanted to reveal the construction behind the home. “You can see how it fits like a hand in a glove. It’s so precise,” he says.
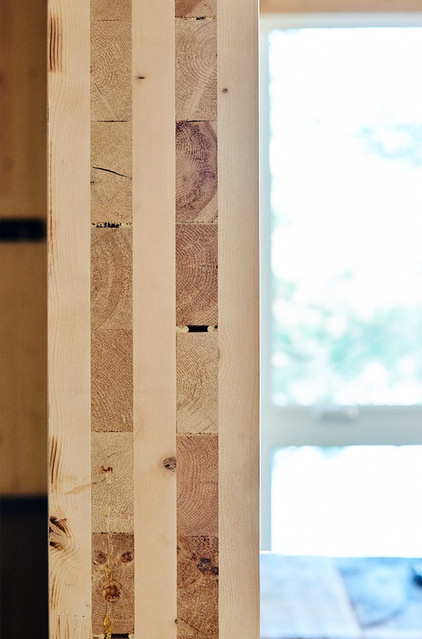
This is what the CLT panels look like from the side. You can see the five layers that form the solid insulation.
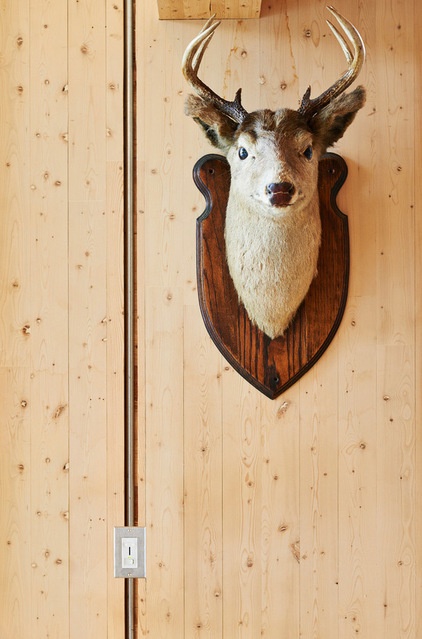
Here Kariouk recessed the light switch but left the conduit exposed for an added ornament.
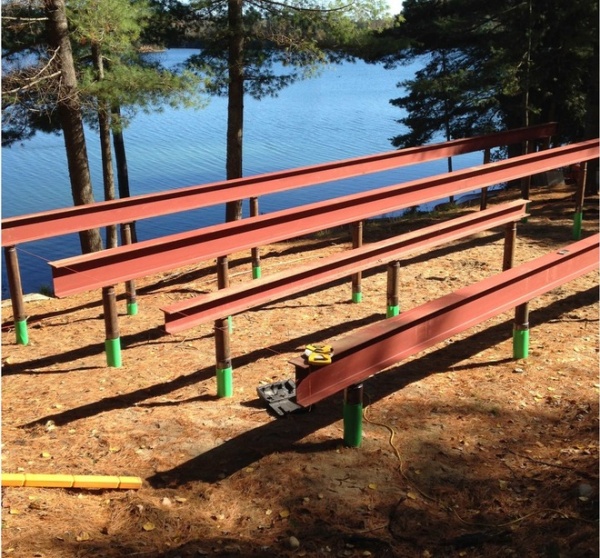
For the construction, 20 8-inch-diameter steel columns were screwed into the ground until they reached bedrock.
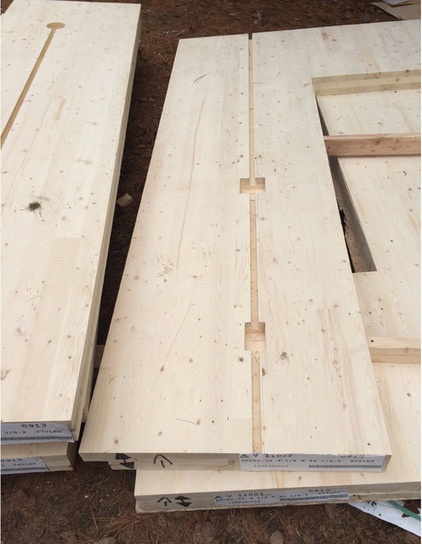
Kariouk and his team spent about a year designing the home, making sure each CLT panel was planned accordingly. For example, because the panels are multiple layers of wood totaling 6 inches thick, none of the plumbing or electrical could be run through the walls. So, whenever possible, Kariouk had to plan ahead and route conduit niches into the panels, as shown here.
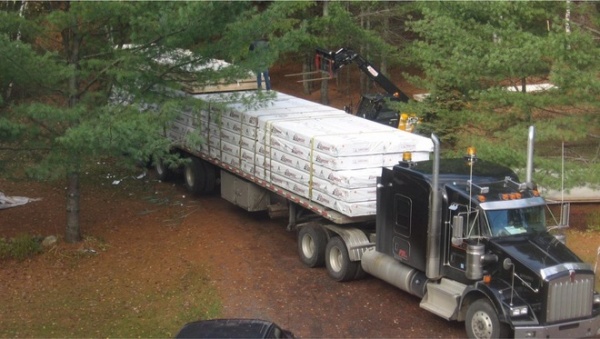
The panels were then delivered to the site on a flatbed truck.
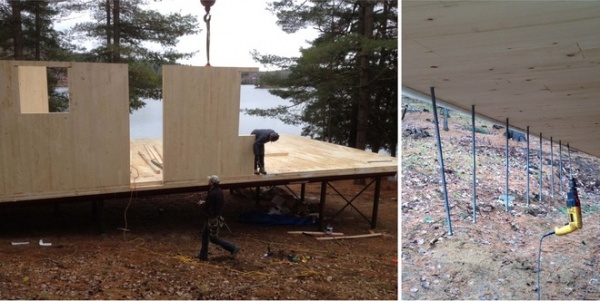
A crane lowered the panels into place, and they were snapped in and screwed together, forming the skeleton of the home in a couple of days. The rest, like the plumbing and electrical, took a few weeks.
Kariouk says the cost for this type of construction probably is about the same as the traditional method of lumber framing, but this method is a much higher-quality form of construction that will last longer.
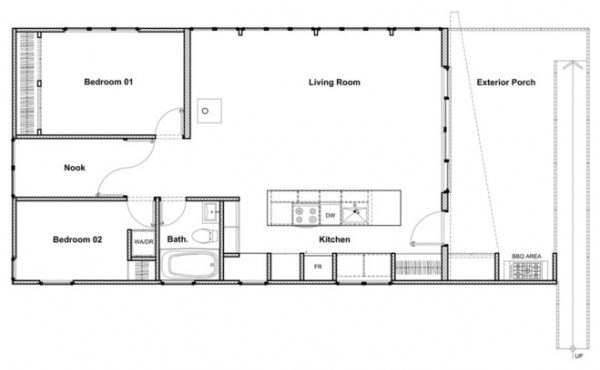
Here you can see the overall layout of the rooms, which stayed within the 1,000-square-foot footprint of the original cottage.
Mulvagh estimates that the project cost was about $400,000, with the CLT material accounting for about $80,000 of that. “For us it was a really affordable way of building something that’s just a summer home,” he says. “It’s durable, has good insulation, and it’s interesting to look at.”
Architect: Paul Kariouk, Kariouk Associates
General contractor: Gilles Langlois, GPL Construction
Browse more homes by style:
Small Homes | Colorful Homes | Eclectic Homes | Modern Homes | Contemporary Homes | Midcentury Homes | Ranch Homes | Traditional Homes | Barn Homes | Townhouses | Apartments | Lofts | Vacation Homes