Insulation Basics: Natural and Recycled Materials
http://decor-ideas.org 10/08/2014 21:13 Decor Ideas
Natural insulation materials, like wood fiber, expanded cork and sheep’s wool, tend to be more expensive than their more commonly used counterparts, such as fiberglass, polystyrene and rock wool. But they have a couple of advantages over synthetic materials and mineral wools that may outweigh the higher cost. Here’s what to consider when it comes to your insulation choice.
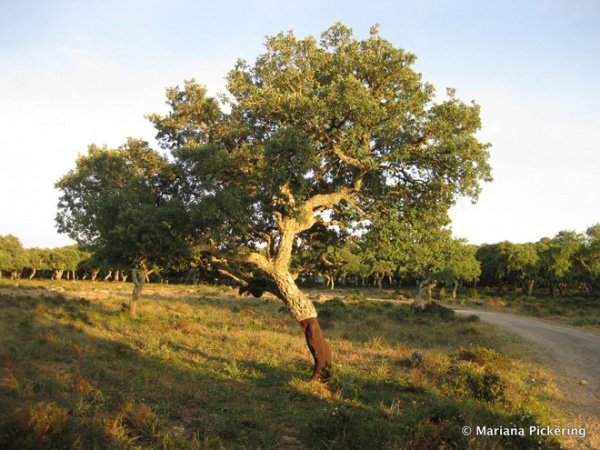
First of all, natural insulation materials, like cork oak (Quercus suber), pictured here, tend to have low toxicity levels and are theoretically better for the environment and your health. I say “theoretically” because, as with all products, quality and purity vary, and it’s important to do your research and know what you’re getting. Especially in today’s age of greenwashing, you need to be attentive to manufacturers’ claims of a product’s being ecofriendly. Some natural insulation materials may contain glues or binders that emit toxic chemicals, just like standard insulation materials, making it not very cost effective to spend the extra money to go natural.
With any material claimed to be ecofriendly, always ask these questions: How do you source the material?Were any glues or binders used?How is it treated for fire and insect resistance?Is your product guaranteed by any third-party certification?
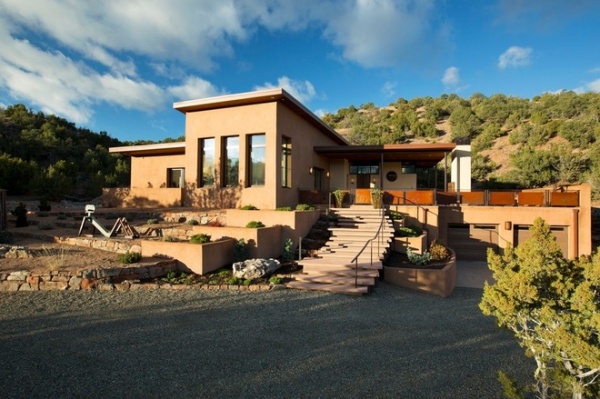
Second, natural materials have a characteristic that is beneficial for increased comfort in the summer or in a heat wave. They have a higher thermal capacity than synthetic materials and mineral wools.
Now let’s run through the basics of some of the most common natural and recycled insulation materials, to get a better understanding of them.

Sheep’s wool. Depending on where you are located, you may be able to find wool batts manufactured from textile-industry wool waste, wool sheered directly from sheep or wool chemically removed from organic lambs slaughtered for meat. Some ambitious DIYers purchase, clean and treat sheep’s wool themselves, which may actually be a cheaper option if you happen to have access to a lot of sheep.
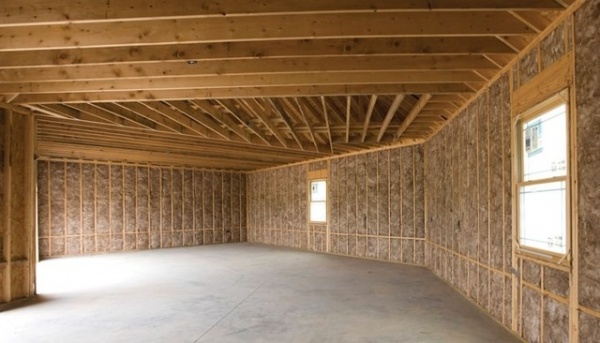
The ability of wool to absorb moisture makes it particularly interesting for some applications, but repeated absorption and release may cause the borate — which makes it fire and insect resistant — to leech out.
See more on designing for temperature extremes in any season
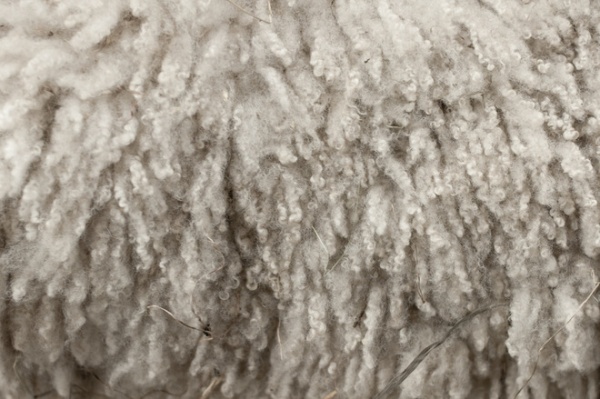
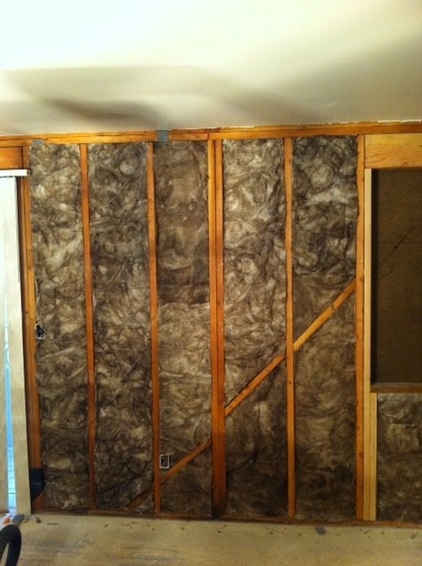
Sheep’s wool is a great insulator. It’s very efficient and naturally able to handle condensation. It doesn’t clump or settle over time, and it actually can have an air filtering effect, because it has the ability to absorb some airborne chemicals, such as formaldehyde.
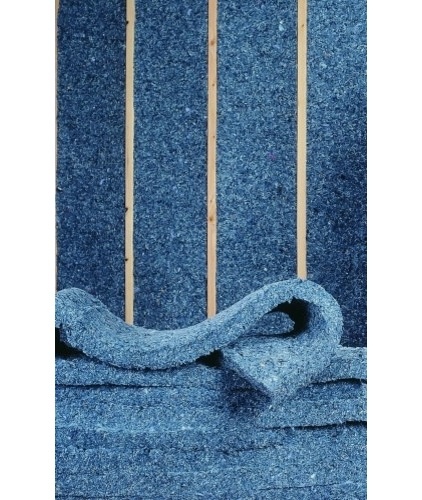
Recycled textiles. Postindustrial recycled blue jeans and other forms of fabric from the textile industry are finding new purpose as cotton insulation batts. Less common in Europe but gaining popularity in the U.S., these batts are comparable to fiberglass in performance and format but contain no formaldehyde.
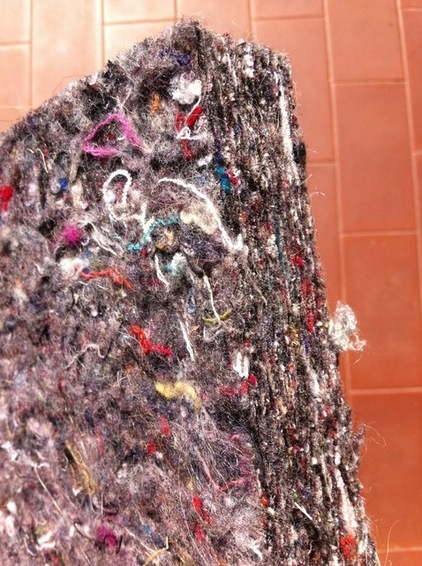
The recycled content is usually around 85 percent, with the rest being polyester. The installation is a little more difficult, in that it’s harder to cut the batts accurately, but there are no health risks, the material doesn’t make you itch when you touch it, and a respirator isn’t necessary.
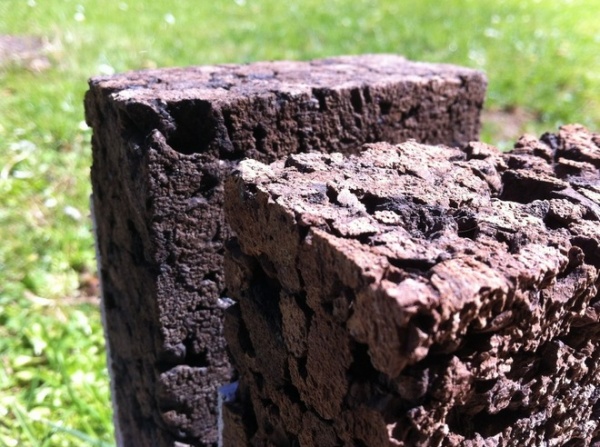
Expanded cork. Cork is perhaps the most efficient natural insulator and one of the most durable natural-fiber insulation options available, but often also the most expensive.
There are no synthetic glues used to bind the cork granules into boards. Instead, the granules are heated and the suberin, a natural substance of the material itself, binds it together. Cork can be divided into boards of varying thicknesses.
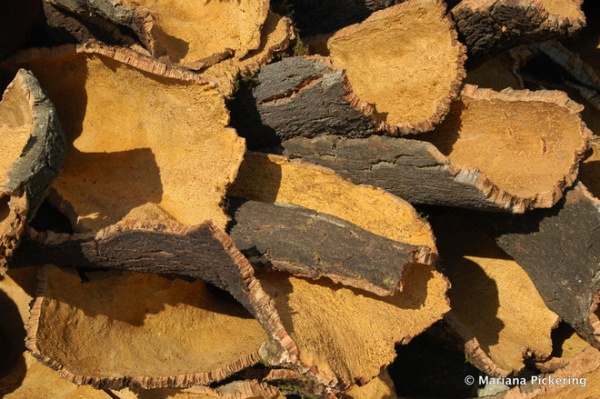
As always, there are advantages and disadvantages to every material. Cork, however, has good thermal performance for both cold and hot temperatures.
While cork has been used for quite a while in Europe as a rigid insulation material, the American market will need some time to learn how to work with this relatively new material. As with many rigid insulation materials, it can be difficult to avoid gaps at the joint of the boards, so you will want to overlap the material and pay special attention to tricky spots, like around windows.
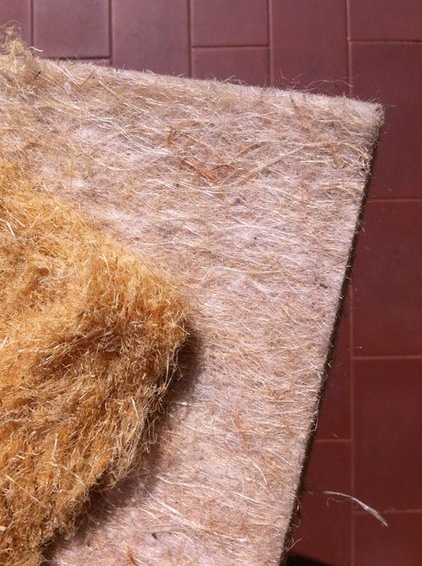
Wood and hemp fiber. Wood fiber (seen here on the left; hemp fiber is on the right) is commonly used in Europe, but arrived on the American market (as far as I can tell) only a couple of years ago. It often comes in the formats of flexible batts or rigid boards, but can also be found as loose fill. Boards that are made with the wet process use heat and pressure to naturally bind the material into boards, but may include additives to protect against moisture. The dry process, on the other hand, may include the use of a synthetic binder to form the boards.
One of the major risks with this material is its high flammability, and if not installed correctly, it can pose a danger. That means you would need to be all the more vigilant about finding an installer who is willing to try it out and perhaps be open to the idea of having it inspected for peace of mind.
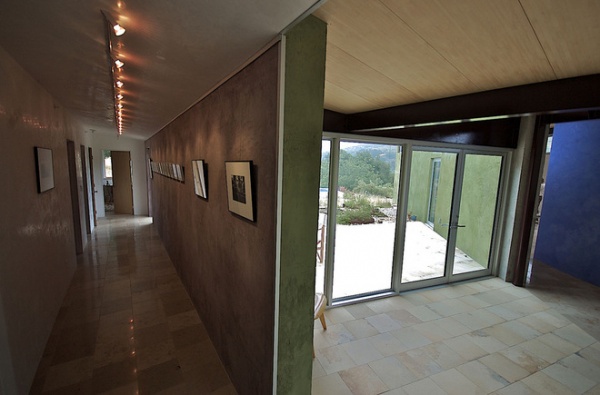
The advantage of wood-fiber panels is their high permeability, similar to mineral wools, allowing water vapor to pass through easily. For people particularly concerned about their wall assembly’s not holding any moisture, this could be an interesting solution.
Hemp fiber has similar properties but is a more rapidly renewable resource and has a lower density (performing not quite as well as wood fiber in summer conditions).
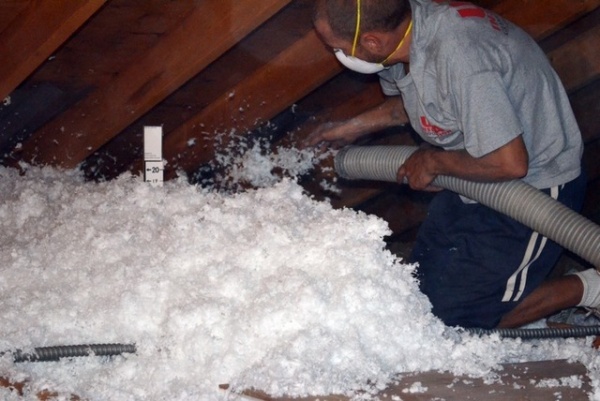
Cellulose. Cellulose has been in use as a loose-fill insulation material in some regions for a few decades now. It is basically wood fiber farther down the food chain, after it has become sawdust or discarded paper.
Depending on the manufacturer, this material can be composed of recycled newspaper or sawmill scraps, but there are also manufacturers who use virgin wood, which is unfortunate, because they are downgrading a valuable material to a job that could easily be fulfilled by wood that has already served other purposes. Even the recycled-newspaper cellulose gives some people pause because of the ink content. In Europe sawmill cellulose can cost up to 30 percent more than other kinds of cellulose based on these concerns.
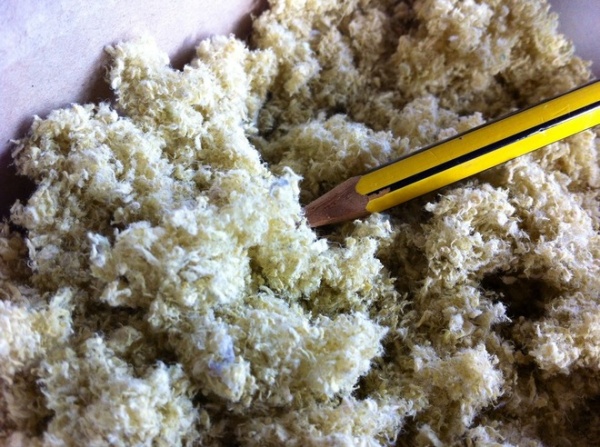
Because it is blown into place, there are no binders or glues to worry about. (Note that I’m referring to dry blown-in cellulose here.) There are also damp-spray, netted and dense-packing methods. Some people report that it settles over time, but if it is properly blown in, settling is very limited or even nonexistent.
We often recommend that the installer’s work be quality checked during the process by a third party with an infrared camera. This ensures quality of installation for an relatively low hourly cost, possibly avoiding the future cost of fixing or redoing the job.
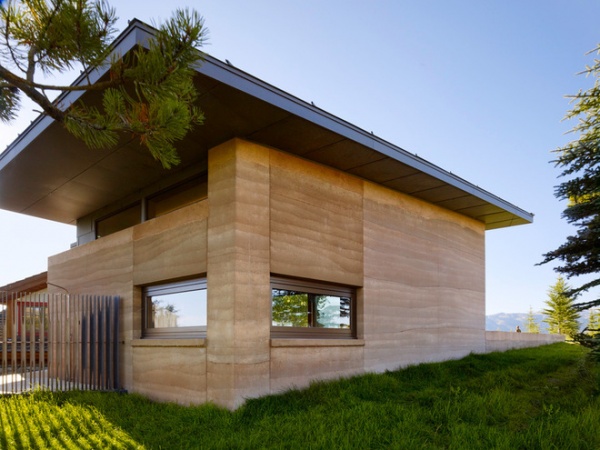
Earthen and straw bale construction. Other natural wall assemblies include straw bale construction and various types of earthen construction.
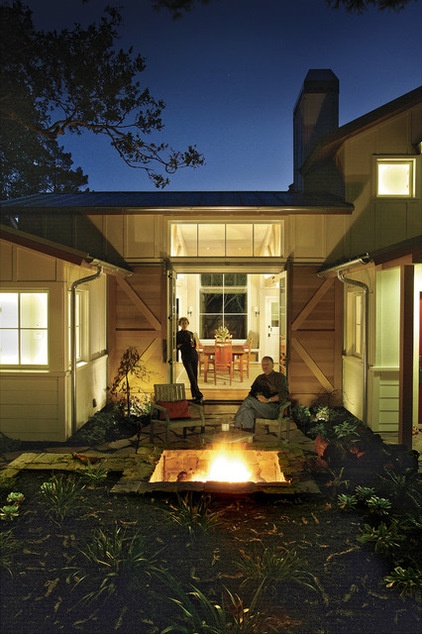
Do your research. With all of these materials, your installer should be aware of how to properly seal the insulation from fire hazards, like a chimney and light casings. None of these materials acts as an air barrier, and proper attention to air leakages should be addressed before you even worry about insulation.
See more on getting cleaner indoor air
Related Articles Recommended