Houzz Tour: Meet a Home Made With Minivan Parts
I’m not sure if Lee Iacocca sent him, but architect Karl Wanaselja spent countless hours searching car junkyards for America’s best-selling Dodge Caravan minivan. Fascinated by finding ways to use junked car parts in architectural designs for more than a dozen years, he got a good system down while searching for parts to build the home he shares with Cate Leger and their daughter, Chloe.
On a pretty good day, he’d map out the junkyard for the cars with roofs in the colors he was seeking. Then he’d strap on his protective gear to spare his eyes, ears and hands, and cut out eight to 10 car roofs with his Sawzall. At the same time, he’d seek out clear Caravan windows. He’d carefully stack the salvaged pieces in his wheelbarrow, placing floor mats between them for protection, then check out and bring his haul to his metalworker. By the time the house was finished, he had used 104 car roofs and 41 windows on the house, which is a constant work in progress.
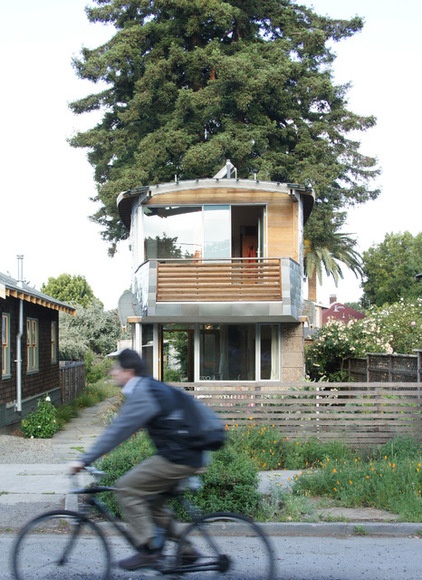
Houzz at a Glance
Who lives here: Architects Cate Leger and Karl Wanaselja and their daughter, Chloe
Location: Berkeley, California
Size: 1,140 square feet (106 square meters), 2 bedrooms, 1½ bathrooms
Photos by Leger Wanaselja Architecture, except as noted
The home’s shape was influenced by the orientation, existing redwood trees on the site and setback restraints, and a desire to keep the neighboring home (left) from being too shaded. The result is a house that ranges from just 14 to 17 feet wide and has a curved roof.
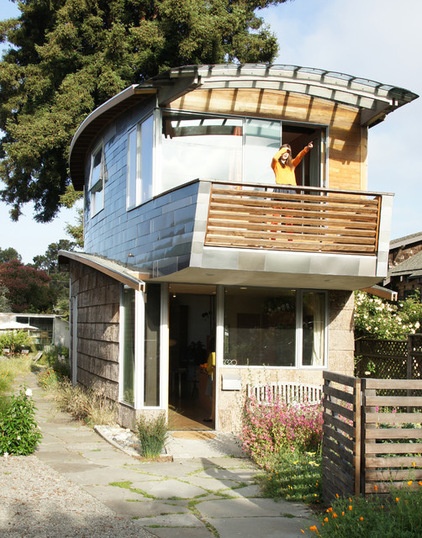
The home’s exterior is an assemblage of pieces that otherwise would have gone to waste. Saving the car roofs before they were crushed saved the energy it would have taken to recycle the metal. The poplar bark siding on the first floor is a waste by-product from the furniture industry in North Carolina.
All of the wood used on the exterior railings, siding, fence and decking is salvaged redwood. Wanaselja likes to use all the leftover pieces of wood from his projects to reduce construction waste. “I’ve figured out how to make use of pieces as small as 6 inches long,” he says. “It’s one of those fun design challenges.”
Bark siding: Bark House
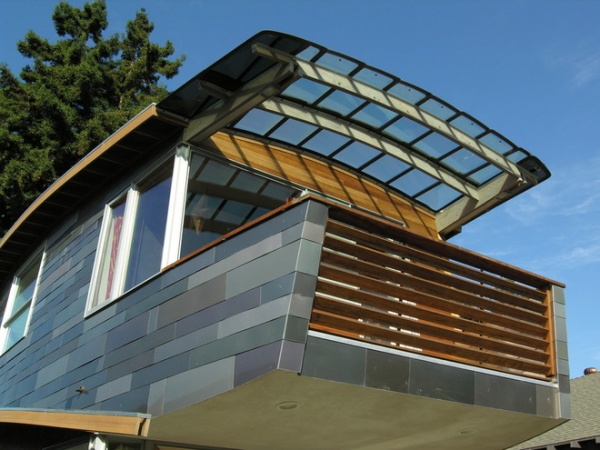
With all of the work involved in procuring the car roofs, one might wonder what drew Wanaselja to them in the first place. For one thing, the range of silvers and grays he chose came together like a painting in a beautiful pattern that shimmers like fish scales. The roofs are sturdy too — the paint is durable, and the metal is a heavier gauge than other metal siding products.
Concern for the environment was another driving factor. “The car junkyard is a tough world; it’s the last weigh station before these cars are crushed,” Wanaselja says. “Generally, they sit for 30 days, and then they are gone.” Most of the junkyard workers had never seen someone who was interested in roofs, so he was able to score them for around $10 to $15 each. The total cost of the salvaged car parts was around $1,500.
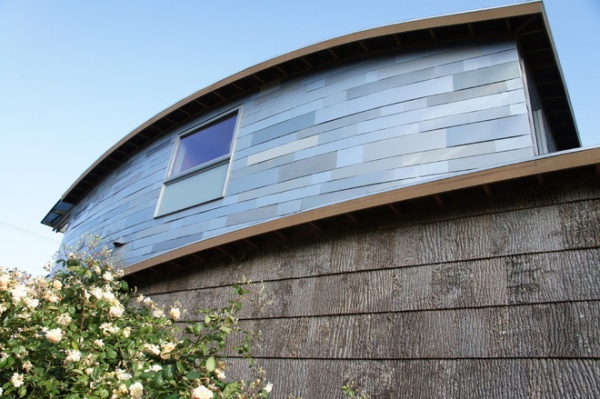
Wanaselja took the car roofs to his metalworker, who sheared them into rectangular shingles of three different widths. The lengths were determined by how large the car roofs were. The edges were painted to prevent rust, then the pieces were cleaned and waxed.
The architect laid out six to eight pieces at a time and then tacked them up with single screws. Working from bottom to top so that the siding would shed water properly, he would step back on the scaffolding and make adjustments to get the pattern just right.
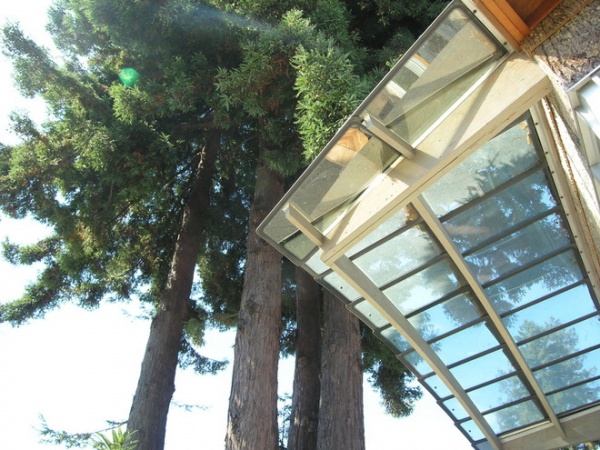
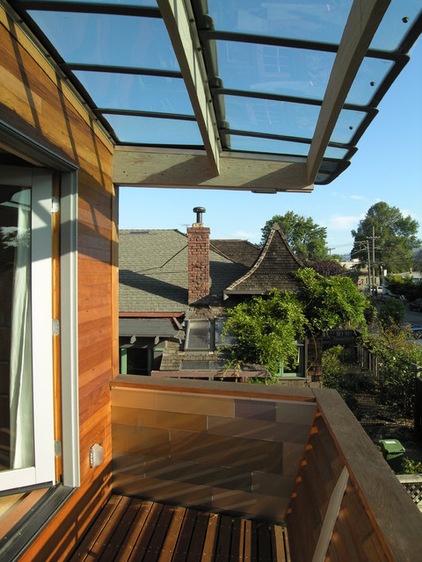
The awnings are made of Dodge Caravan minivan windows. Complicating the search was finding clear, untinted windows, which Wanaselja liked best for the job. There was no easy way to have any junkyard contacts call him when Caravans rolled in; it was simply the luck of the draw when he arrived each time.
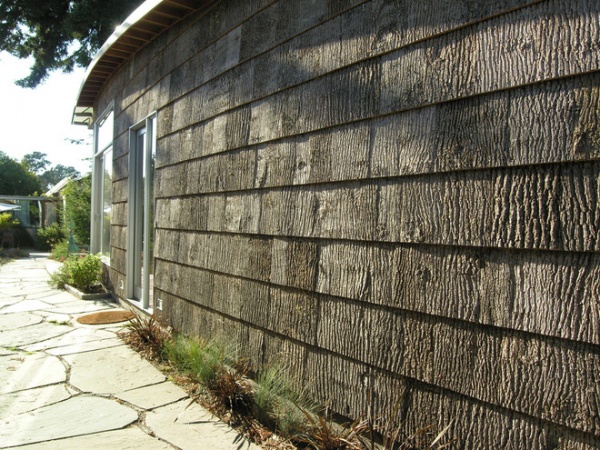
The side that faces the neighbor has fewer windows for privacy. This path is the commute to his firm’s office in a repurposed refrigerated shipping container in the backyard.
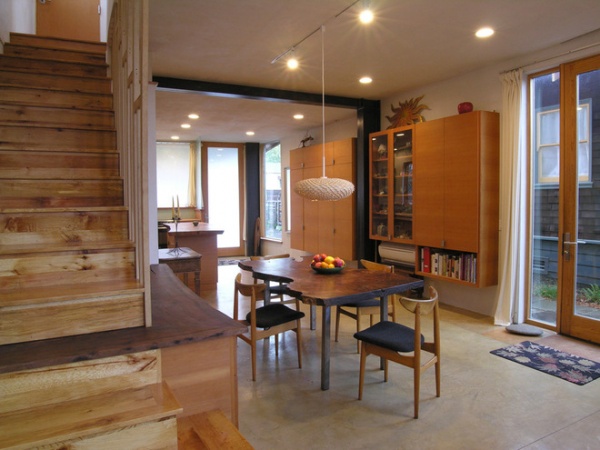
The cabinet wall on the right makes good use of the privacy wall seen in the previous photo. The cabinetry was made with lumber certified by the Forest Stewardship Council (FSC). All of the woodwork and exposed steel beams are finished with a natural linseed oil–based coating from Bioshield.
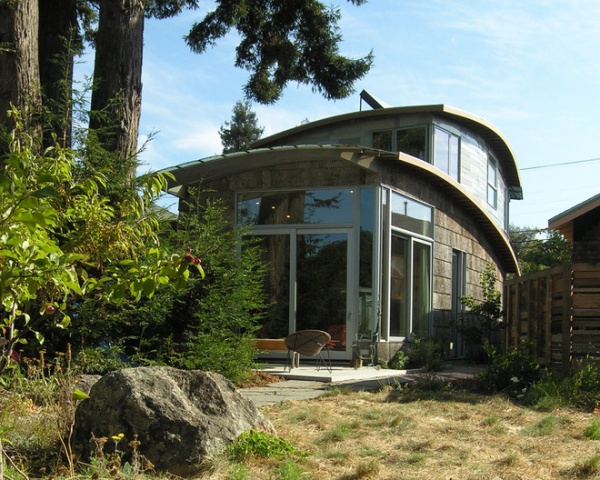
The back of the home faces west and south, which helps warm the house naturally in winter. The backup heat rarely clicks on — it is needed only when it rains or during heavy overcast periods in winter. All the walls and ceilings are made of thick unpainted plaster, which also adds to the thermal mass. While the winter sun warms the house, the overhangs block it from hitting it in the summer. This buffers temperature swings on warm days. The family opens up the house to let in the cool night air and closes the appropriate doors and windows to keep the cool air in on hot days.
The home’s overall energy performance is 43 percent better than required by California’s Title 24 energy code, Wanaselja says. He and Leger chose drought-tolerant, mostly native plants to limit the need for irrigation.
Learn more about passively heated and cooled homes
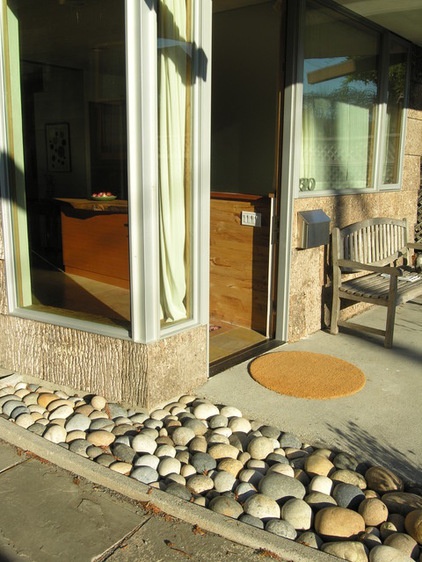
They designed their gutters to collect rainwater in salvaged oak wine barrels, collecting about 1,200 gallons of rainwater per year. The house is plumbed for greywater, which allows them to reuse about 3,000 gallons a year.
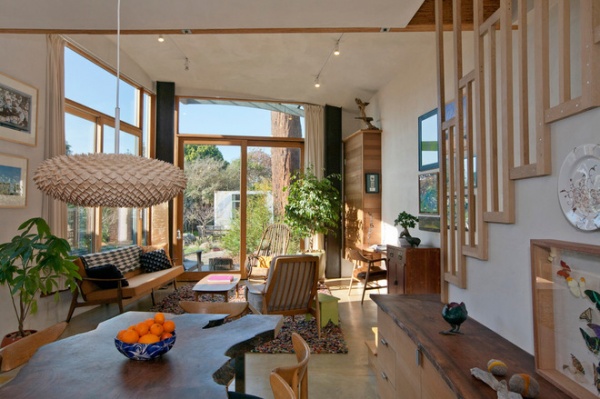
Along with an open plan, the large windows, doors and transoms and the views they provide make the space feel spacious.
Photo by Kiera Marie Condrey
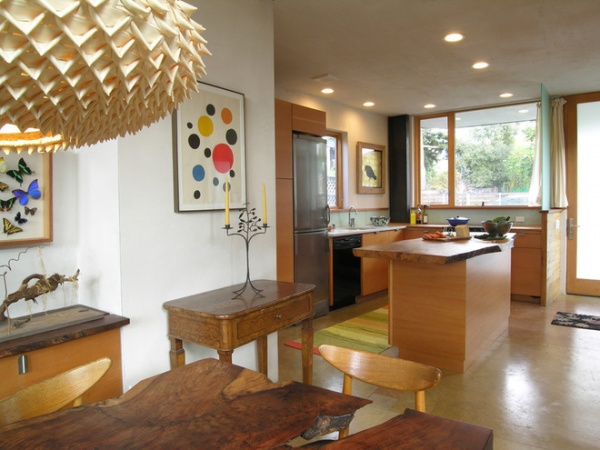
Different woods play a large role in the interior, which the couple is always tweaking; the entire home is a constant work in progress. Sometimes they’ll plan a party just to create a deadline for a project.
Wanaselja and his lead carpenter milled the live-edge furniture pieces seen throughout the home. The wood came from various sources, including a coast live oak that had fallen on property owned by some clients. He milled that tree to use for those clients and then bought a leftover piece from them for the island counter. Some of the walnut pieces came from an orchard in Chico, California, where walnut trees were being replaced.
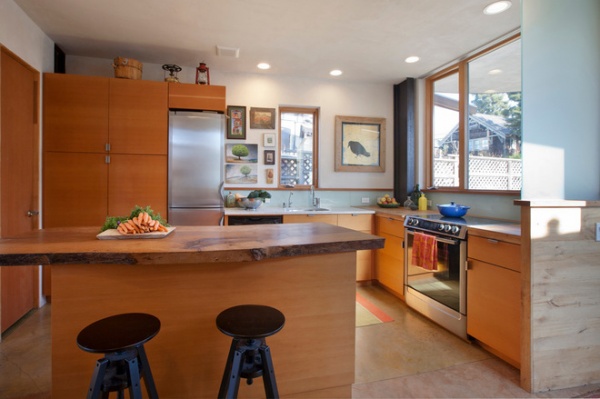
The couple found ecofriendly ways to color and seal their floors as well. Natural earth pigments give the concrete its warm tones; it is sealed with a soy-based binder and a water-based sealer.
The couple used blown-in cellulose insulation, a solar hot-water heater with a backup tankless water heater, and dual-flush toilets. The appliances are all Energy Star rated or better; the interior doors have Kirei Wheatboard cores; and all of the concrete used on the floors contains 50 percent fly-ash cement.
“It’s not about what you spend,” Wanaselja says of the look and function of his house. Well, money-wise anyway, because he certainly paid in time in dusty junkyards and sweat over hot metal. “I said I’d never do it again, but looking back it was like a party … I’d just get into Zen mode and take it at my own pace,” he says.
Photo by Kiera Marie Condrey