Houzz Tour: A New Look for Prefab, Tailored by Local Craftspeople
Imagine if every time you wanted a new shirt, skirt or pair of pants you had to go to a tailor and have the piece custom made. If this were the case, our clothes would be frightfully expensive and certainly wouldn’t be readily available. To overcome these drawbacks, the clothing industry has created a middle ground where clothing items are mass produced to achieve economies of scale. With a little alteration or some personal accessories, you can then easily customize an outfit yourself. Basically, you can have the best of both worlds.
So what happens when the same approach — the efficiencies of factory production combined with site-specific craft — is applied to the creation of a custom home?
I imagine it’s a lot like the Casabrava home by architect Heather Johnston. She took this best-of-both-worlds approach by purchasing a prefab, factory-built home and having it tailored by skilled, local craftspeople. By doing so, she got a speedily built home that looks like anything but off the shelf.
Photography by Brady Architectural Photography
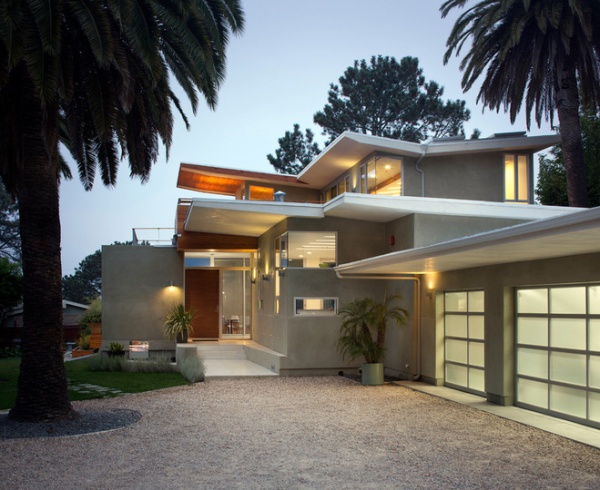
Houzz at a Glance
Location: La Jolla, California
Who lives here: Architect Heather Johnston, her husband and 2 dogs
Size: 3,100 square feet
The design pays homage to Southern California midcentury modernism, a style Johnston enjoys. The main modules of the home were fabricated in a factory offsite, then delivered and assembled in about two days. Local craftspeople then spent about three months adding custom elements. The home was fabricated, assembled and finished in eight months, which saved Johnston 10 to 12 months and helped reduce costs associated with a construction loan, rental housing and more.
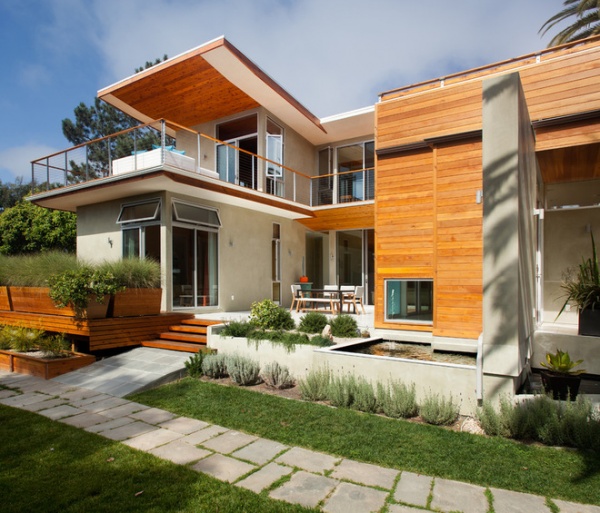
To create soaring roof planes and multiple outdoor rooms, all trademarks of the California style, she had the factory ship the roof elements as separate pieces for placement on the modules at the site. Usually in the typical prefabricated house, the modules are shipped with the roof structure already attached, an approach that can limit the size of the roof heights, overhangs etc.
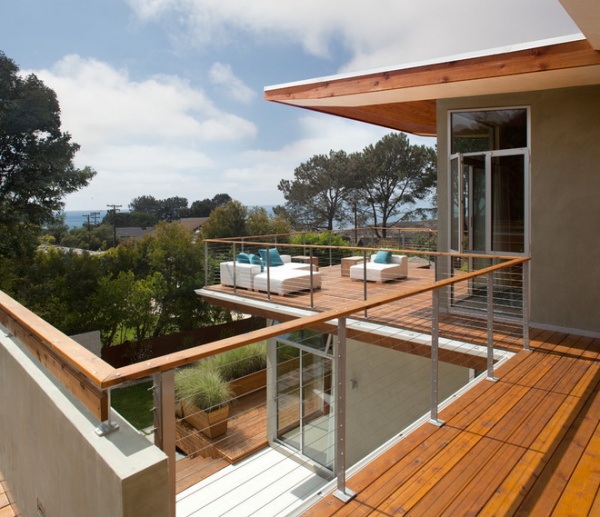
Creating a “sunset and cocktail deck” sheltered by the big roof was then possible. With an elevated view out to the Pacific and the sense of shelter created by the roof hovering overhead, this deck is the perfect perch on which to unwind and relax.
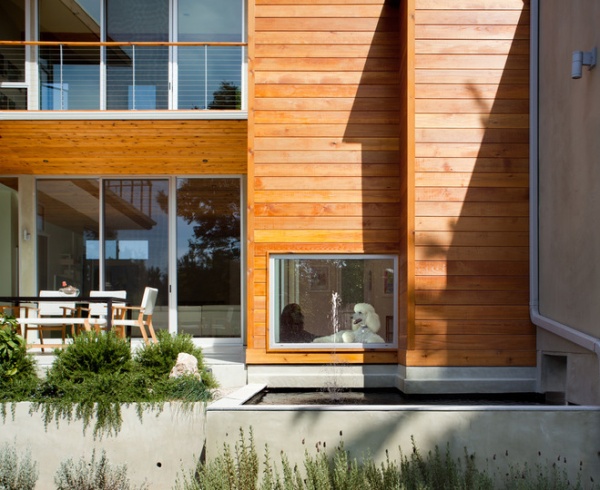
Getting a special bottom corner window for the couple’s two dogs was easier with the prefab process. In a factory environment, workers can use equipment to lift the entire assembly to install things like windows in odd spots. That way no one is attempting to cut, line up and install something while on their hands and knees.
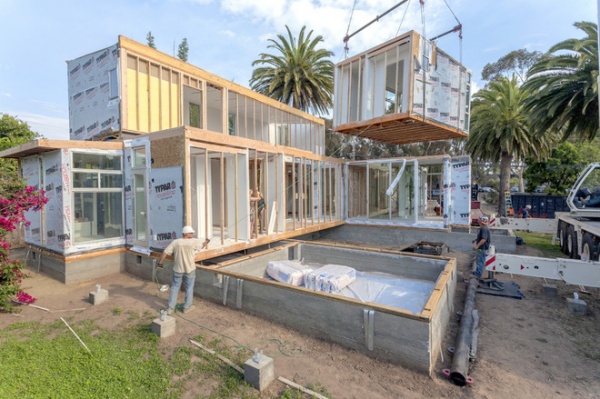
Watching the modules being lifted and put in place at the site gives real insight as to what was produced at the factory and what was to be finished onsite. The structure, electrical, mechanical, windows, drywall and exterior sheathing were all assembled in a factory setting. Exterior and interior finishes such as stucco, siding, wood trim, tile walls and floors, and painting were all completed onsite.
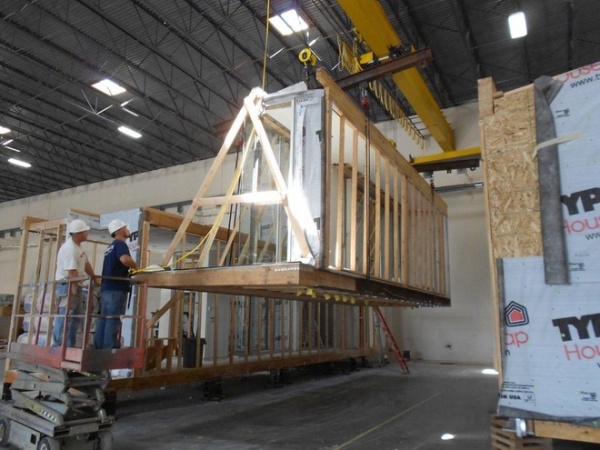
The remarkably short time it took to build the home onsite was a direct result of prefabricating the modules in an enclosed factory, where each piece was built under controlled conditions and then assembled to ensure that everything fit as it should.
Johnston points out that it’s important to interview and get to know the factory where your home will be prefabricated. What are the factory’s capabilities? What is the factory’s workload? What level of quality is the factory able to produce? How will the factory’s idiosyncrasies influence the design? These and more are questions that she asked each potential factory.
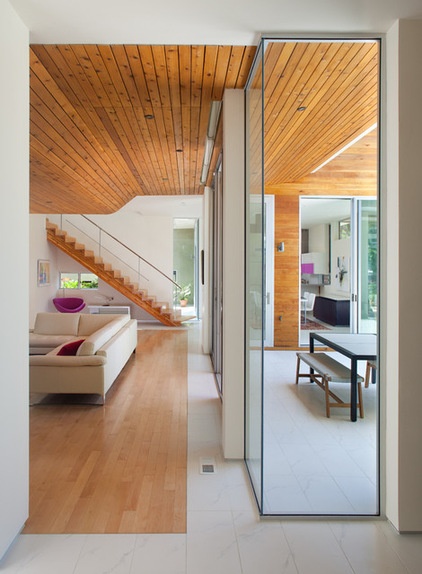
While the modules arrived onsite with the interior drywall already installed, Johnston had most of the other finishes installed onsite, because involving the local building industry was important to her. The tile and wood floors, wood ceilings, drywall finishing etc. were all done by local craftspeople.
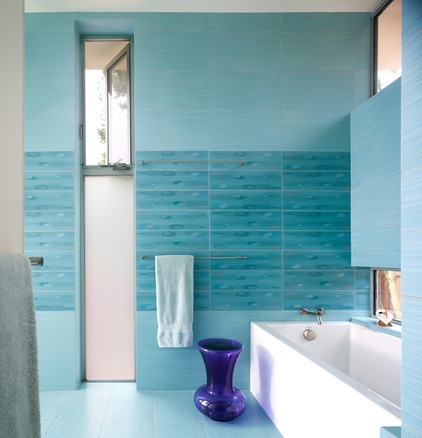
Johnston estimates that the prefabricated and modular approach reduced construction costs by at least 10 percent. These savings as well as leaving areas like the garage unfinished allowed Johnston to splurge on items like tilework, kitchen appliances, cabinetry and LED lighting.
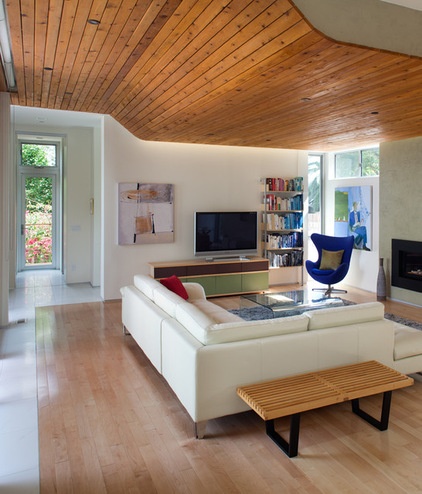
A wood ceiling defines functional areas as well as conceals where the modules meet. Set at 10 feet, 3 inches high in the circulation zone, the ceiling gently curves its way down to 9 feet over the living area.
This ceiling was installed in the field after the modules were set. Doing so enabled Johnston greater design control over this very important architectural element.
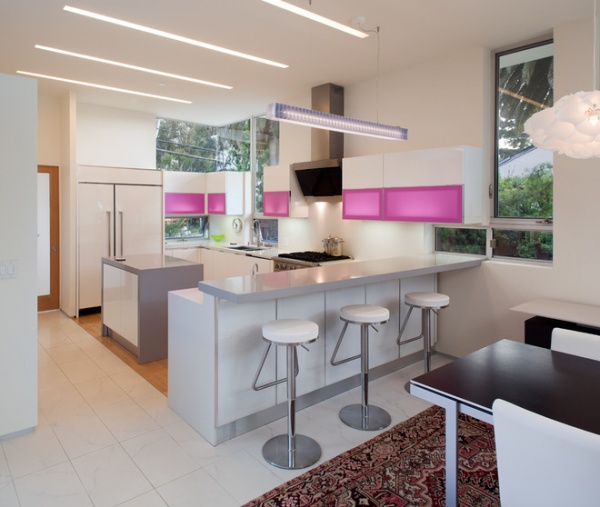
The tile flooring was also installed in the field for much the same reasons. With very tight grout joints between tiles, Johnston wanted to make sure the floor was perfect.
Another field-finished item is the level-5 drywall finish. A level-5 finish is the smoothest and most labor intensive of all the drywall finishes, because it requires that the entire surface have a thin skim coat of joint compound (or another similar material) applied. This level of finish is the best when a semigloss or gloss paint is used and will prevent any drywall joints from telegraphing through.
The purple cabinetry is a fun detail. The color was achieved by applying an easily removable and replaceable film over the cabinets. When Johnston gets tired of purple, she can change it without having to change the cabinets.
More: My Houzz: A Prefab Modern Farmhouse Rises in Vermont