How to Commission Custom Wood Furnishings
http://decor-ideas.org 12/29/2013 07:23 Decor Ideas
My technology-driven husband has been working with concrete for years on his off-hours to fulfill his creative side. His efforts are leading up to his finishing a fireplace surround from scratch. When he’s done with it, he’s going to need the perfect wood mantel to complete the job. As comfortable as he is with concrete, neither he nor I have a clue what do about the wood component. It has to be custom, but where to start?
“You write for Houzz,” he said. “Your job is to find this stuff out.” He was right. I went to two woodworking experts to get the insider information that can help you, too, understand how to get exactly what you want in a custom wood piece.
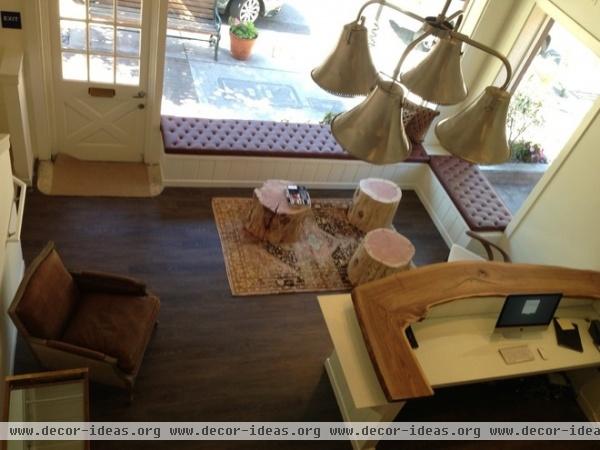
What do you want to customize? The possibilities are almost endless. Aside from mantels, you can commission dining tables, desks, console tables, coffee tables, occasional tables, outdoor tables, benches, chairs, headboards, built-in media centers, architectural details and sculptural pieces. “Just about anything a client can dream up,” says San Francisco woodworker Colleen Smith, “a skilled woodworker or furniture maker can create.” Smith created this custom elm reception counter and redwood stump stools for a client’s salon in Saratoga, California.
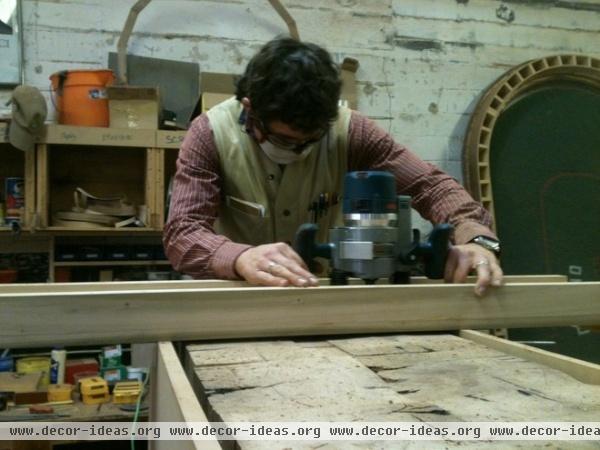
Find the right woodworker. Each artisan has a different skill set. “Some people are experts in crafting fine furnishings, while others excel in rustic pieces,” Smith says. “It’s important to search out an artist that specializes in your desired type of project.”
Referrals are a great way to begin your search. If you see something that catches your eye, find out who made it. Then seek out more examples of that professional’s work through a website, Houzz profile and press coverage. If the woodworker is local, visit the shop if you can.
The human connection. Artisans are usually a one-person operation, with maybe a small staff. In this sort of small-business community, it’s common for woodworkers to refer potential clients to other artisans that might be a better fit for a particular custom job.
“Be sure to see how broad the woodworker’s portfolio is,” says Atlanta furniture maker Stephen Evans (shown here working on a commission). “Design and fabrication are about problem solving, and that’s what makes your project, and the work itself, custom.”
Questions to ask:
• How long have you been in the woodworking business?
• How long have you been in business for yourself?
• Have you done something like I’m asking for before?
• What finishes or materials can you recommend?
• How long will it take?
Browse woodworkers on Houzz
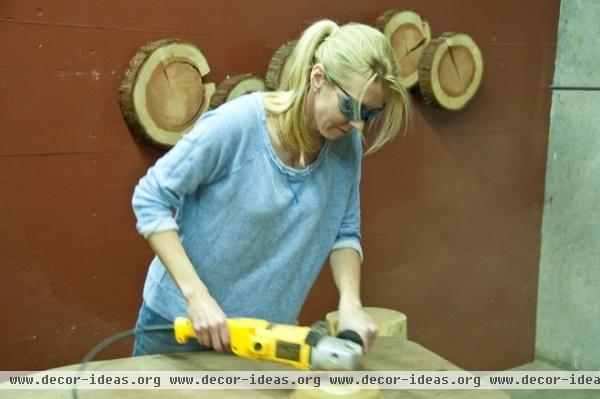
Communication is key. “Sometimes it’s difficult for a client to describe in technical terms exactly what they are looking for,” says Smith (shown here working in her studio). “It’s more a look and feel that they’re going for. A woodworker needs to be able to take the time to listen, ask clarifying questions, show examples and narrow down specifics.”
Once you’ve figured out which person you’ll entrust your vision to, it’s time to work together to devise a plan that includes the size of your project, wood species, finishes, budget and calendar. A good woodworker will help you make decisions and, if need be, isolate the critical factors in the project
Tip: Make sure to read the contract outlining what to expect, how payment is to be made, the delivery date and the costs before agreeing to work with someone.
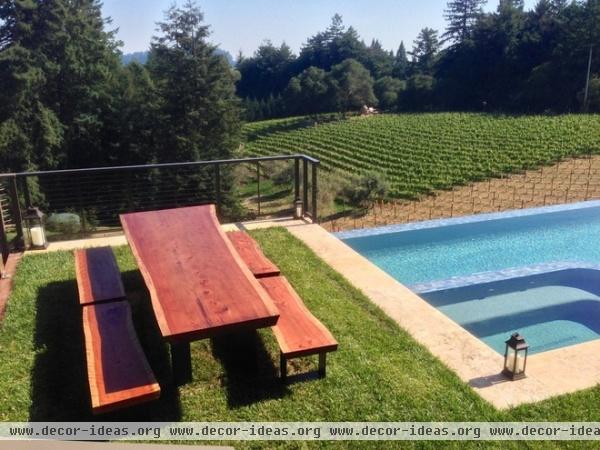
Responsible sourcing. If you’re concerned about where your wood will come from, it’s important to work with an artisan who gets wood ethically and sustainably. “This is incredibly important not only to most of my customers,” says Smith, “but for the longevity of the business and resources in the industry.”
This redwood table and benches, responsibly sourced and crafted by Smith, were commissioned for poolside picnics at a vineyard in Sonoma, California. The base is buried under the grass.
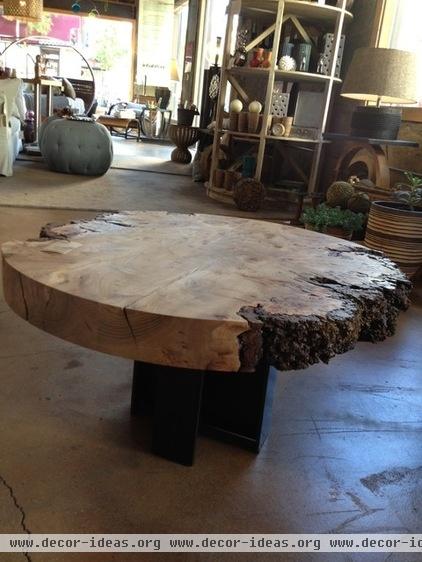
Elm Cocktail Table Cost considerations. “It’s important for prospective clients to understand that custom work is almost always going to be more expensive than comparable retail or commercially available pieces,” Evans says. “The fact that the woodworker must first design the piece, then acquire materials, set up tools, fabricate, finish and deliver means that costs can add up quick.”
Expensive doesn’t necessarily mean better, he cautions. “There is a point in custom design where your attempts at saving money begin to cut into the benefits of custom design — namely, custom sizing, function, styling,” he says. “To avoid this I suggest researching comparable items in the marketplace. Next take this information and visit a custom shop so you can review your desires against the realities of the build.”
A good woodworker will be able to help you construct a budget so you can be sure of getting the most for your investment.
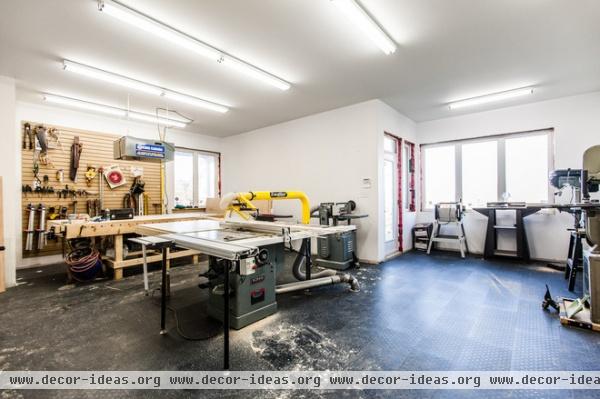
Don’t expect a rush job. Allow anywhere from six to 16 weeks for delivery, depending on the request. “People have to understand that woodworking is not easy,” says Evans. “Weather can affect production, as can illness, tools breaking, having materials on back order and, of course, sourcing the right wood and allowing it to dry.”
One of your goals should be for this piece to last a long time. Given wood’s durability, this could be longer than your lifetime. Patience is a small price to pay for this sort of long-term investment.
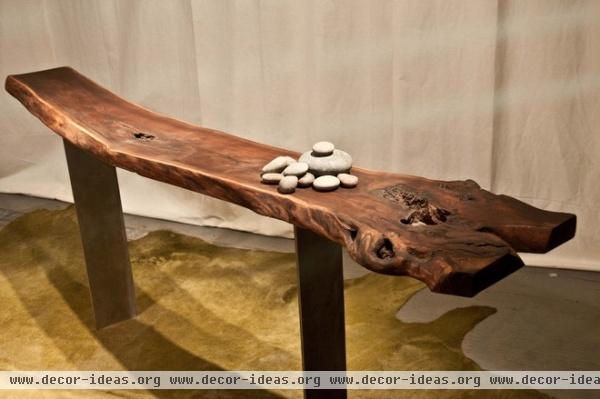
Live-Edge Walnut Console Table Picking the wood species. As if the design itself weren’t exciting enough, choosing the wood’s species part of the process, and customization plays an equally important role here too. Wood types have different characteristics and are suitable for different applications. “There is a multitude of wood species, from local to exotic. The important thing to understand is that hardwoods tend to wear better in high-traffic areas,” says Smith, “and soft woods, like redwood, tend to weather better outside. A woodworker will help steer clients to species that suit the piece’s application best.”
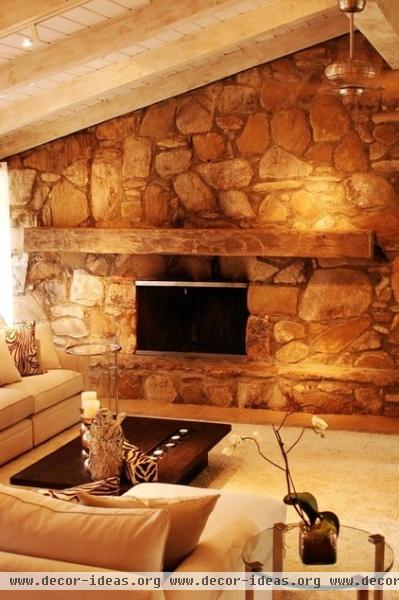
Reclaimed-Wood Mantel Hope this helps you on your quest for a custom wood piece. For our mantel, my husband has his eye on a hundred-year-old beam of reclaimed Brazilian bloodwood that should have a similar rustic feel to this mantel created by Evans. Once we work out the details with our San Francisco Bay Area woodworker, we’re expecting it to take about six weeks to receive the piece to our specifications. We can’t wait.
Your turn: Please show us your custom wood piece in the Comments and tell us how you had it made.
Related Articles Recommended