Prefab Homes Expand Modern Design's Reach
http://decor-ideas.org 11/13/2013 01:10 Decor Ideas
Single-wide, Double-wide, T series, L series, Z series, Lifted Bar, Two-Bar Bridge, Three-Bar Saddlebag. Such is the lingo one uses in the world of New York City company Resolution: 4 Architecture (RES:4 for short). The architects design prefabricated dwellings they call "modern modular," influenced by the interior renovations they carried out on their home turf but also by a strong belief in prefab's ability to provide affordable modern houses. Modern Modular, a new book from Princeton Architectural Press, highlights 14 of the dozens of prefab houses they've realized. This ideabook looks at a handful of those to get at how their modern modular design works and see what the book offers.
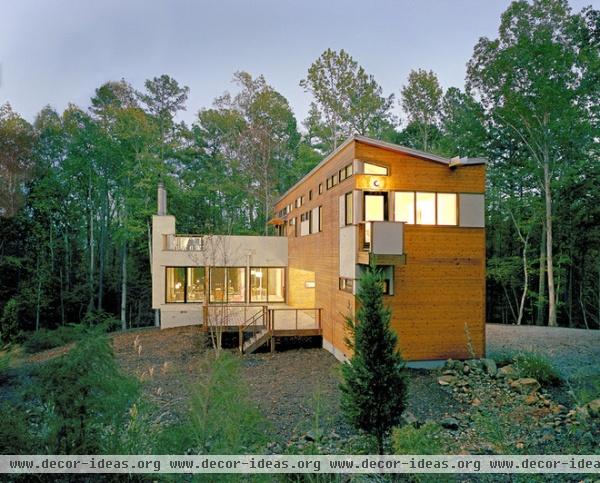
The Dwell Home
Pittsboro, North Carolina
2004
Even though RES:4's Joseph Tanney and Robert Luntz were dabbling in prefab before this house, they burst onto the scene in 2003 when their design was selected in Dwell magazine's challenge to 16 architects to design a prefab house for less than $200,000. Allison Arieff — editor at Dwell at the time and the author of the 2002 book Prefab — penned the foreword to Modern Modular; she recounts how she developed the challenge with real clients. This situation meant that, unlike with many architectural competitions, the house was realized, the first of many to come for RES:4.
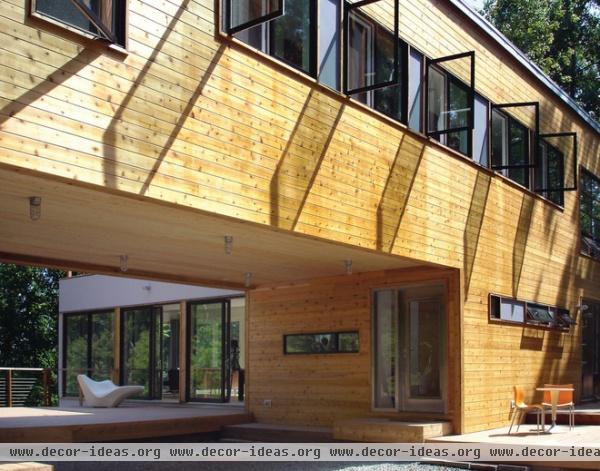
The modules of the "modern modular" homes are rectangular boxes based on a number of factors, but the driving restriction is what the Department of Transportation allows on roads and highways. The maximum width allowed is 16 feet, and the maximum height is 11 feet. The length of the modules is derived partly from what can fit on a truck, but RES:4 indicates that the 60-foot length used is "the optimum length in terms of filling assembly line space — the primary measurement of value in the assembly line methodology." This length allows fairly long spans for carports, entries, shaded outdoor spaces and other potential uses.
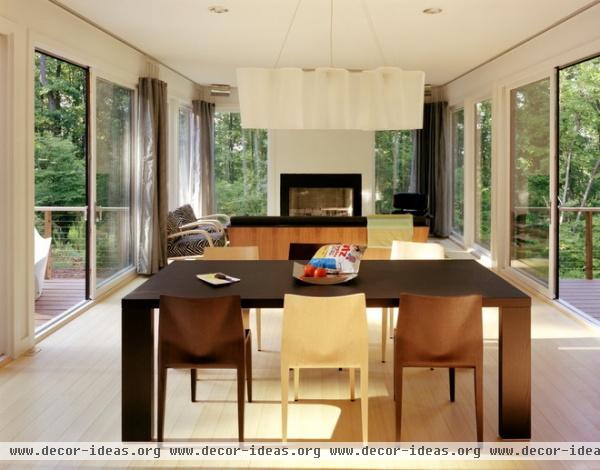
The company's 16- by 60-foot module (which may be narrower and shorter in some instances) works extremely well for domestic spaces: living spaces, kitchens, bedrooms. Inside the second floor of the Dwell Home we can see how there is plenty of room for furniture in the open living space, as well as for the walkways on the side, which provide access to the rooftop decks.
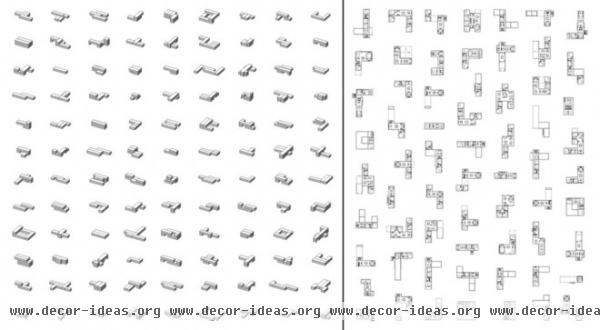
The modules allow for nearly limitless combinations, depending on the number of them (the Dwell Home has five) and how they are combined. Here is where terms like "T series," "L series" and "Z series" enter the picture. The layout and stacking of the modules (left) can follow site and other restrictions, translating into plan variations (right) that respond to the same, as well as the owner's needs. The Dwell Home is an L Series Two-Bar Bridge that is capped by a butterfly roof.
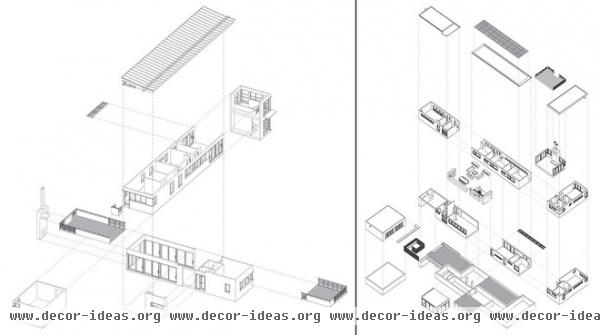
Each of the 14 houses in Modern Modular is documented with exploded axonometric drawings that highlight the kit-of-parts approach to their design and construction. (Imagine the pieces shown here "collapsing" along the dotted lines to get a mental image of the assembled house.) Here we see the Dwell Home on the left and the Swingline, the next house we'll look at, on the right.
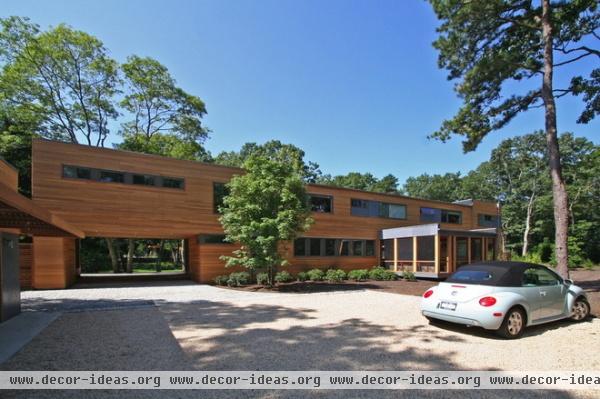
Swingline
Wainscott, New York
2007
While the Dwell Home is made of five modules, Swingline has a total of seven modules (plus a detached garage) in an L, T and Z Series hybrid configuration. Most apparent from the front is how the exterior is primarily solid, to ensure privacy.
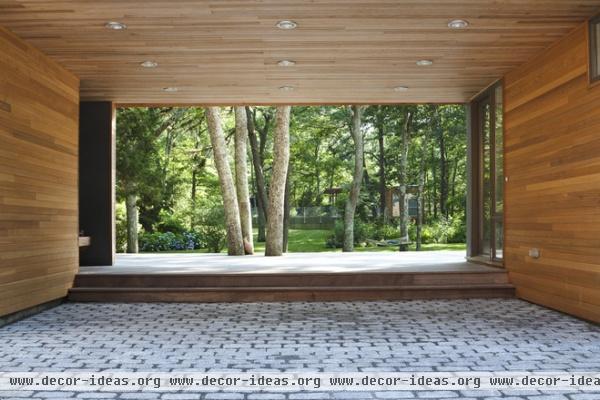
The entry portal, lined in the same wood as the exterior walls, frames a view of the pool house beyond.
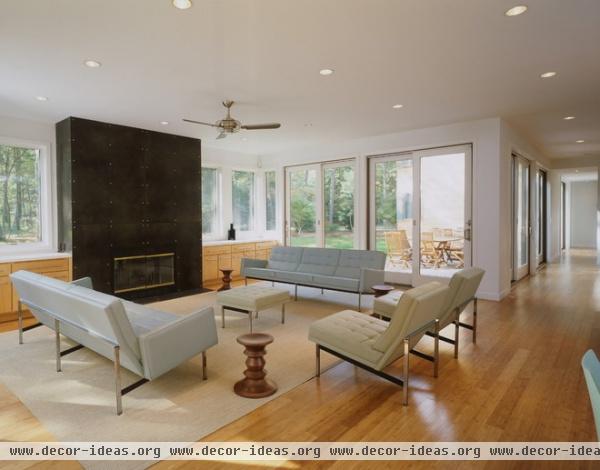
Inside we can see how the private side of the house has larger windows than the front. The flexibility of the modules allows a variety of openings and cladding to be used.
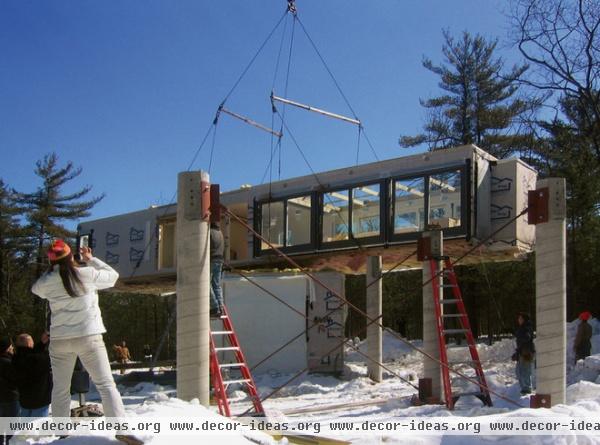
It's worth taking a slight detour to see how these houses are put together. After being assembled in factory conditions (where workers can wear shorts, something they couldn't do onsite), the modules are trucked to the site and lifted into place atop foundations with the necessary mechanical, electrical and plumbing provisions. This retreat in New York's Catskill Mountains, sits atop concrete columns so the living space and terrace are raised above the surrounding trees.
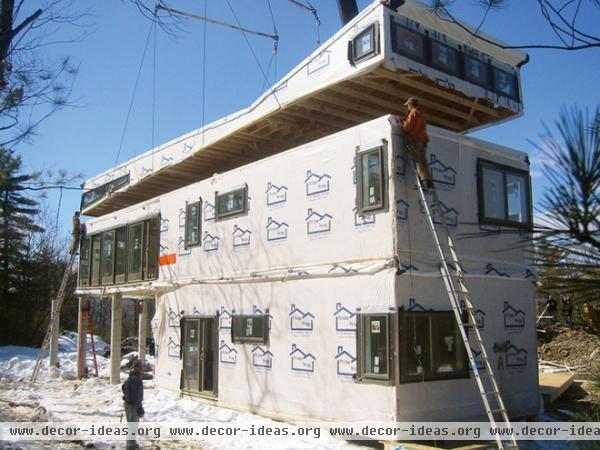
The house is a simple configuration of two modules — one standard size and one shorter — topped by a butterfly roof. Here we see the roof being lifted into place. Given the Department of Transportation restrictions, this and other nonflat roofs need to be built and assembled separately. This one may look small, but it helps in gaining additional daylight and making the open living areas feel larger.
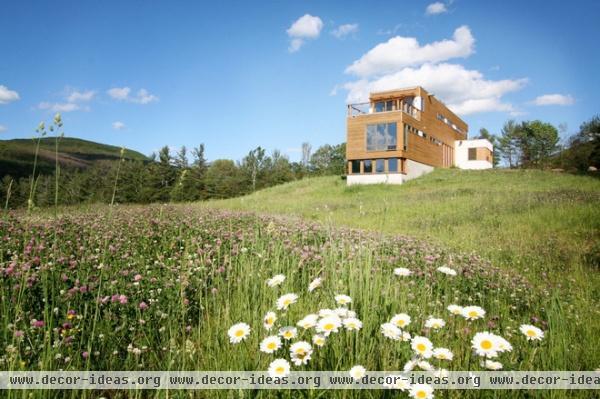
High Peak Meadow House
Maplecrest, New York
2009
This aptly named house, an L Series Three-Bar Bridge configuration, is made from six boxes that are set upon a hill, taking advantage of views and sunlight. The house seems to reach out from this perch toward a distant vista.
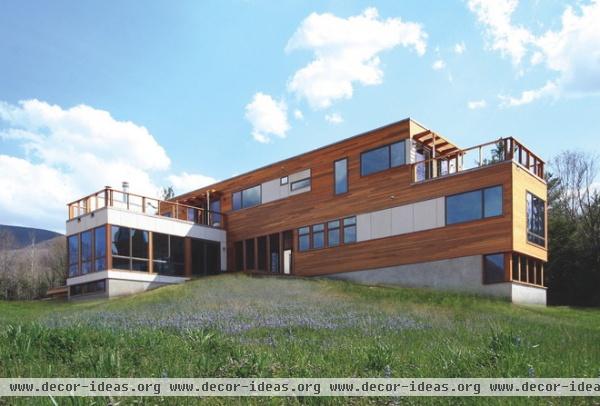
This view illustrates how the exteriors of the modern modules are composed of windows, doors and various solid materials, including wood, metal, fiber cement and, as we'll see, stone. A subtly visible piece of this house is the screened-in breezeway on the middle floor (where the two bars converge), which separates the main house from a separate mother-in-law's house.
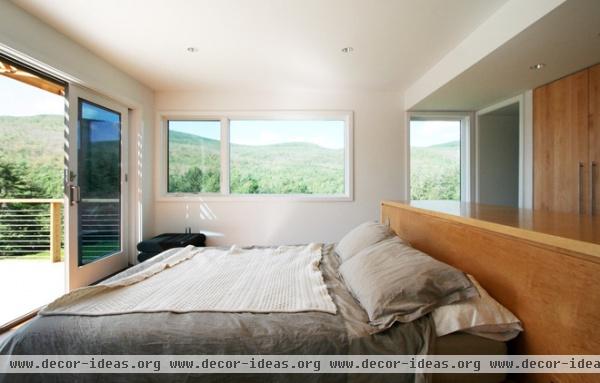
It should be noted that one of the advantages of modular prefab housing is the ability to take care of most of the work in the factory, which translates into quicker lead times and tighter tolerances with materials and finishes. The latter is particularly important with modern designs, where reveals and flush finishes are used in lieu of trim, for example.
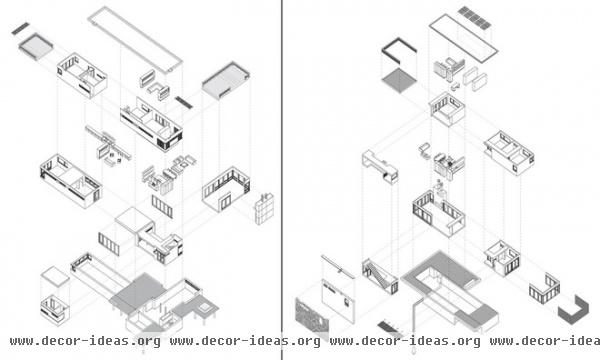
I'll admit that one's eyes can glaze over looking at the exploded axons — shown here is the High Peak Meadow House on the left and the Catskills Suburban on the right — but think about them as three-dimensional blueprints. I could see this being used by the contractor onsite to understand how the pieces should be put together.
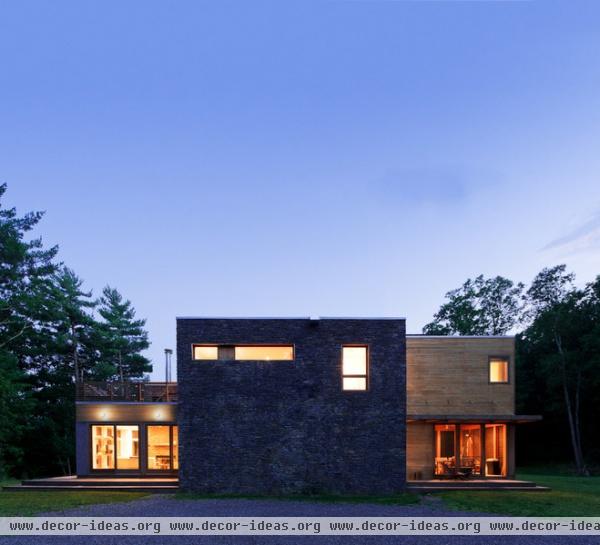
Catskills Suburban
Palenville, New York
2009
The remarkable thing about the modern modulars is how well the design was established from the get-go. The changes to the houses since the Dwell Home was realized are minimal, more refinements than dramatic evolution. But this house in the Catskills points to the flexibility of the process. For one, the modules in the this Two-Story Single Bar configuration were cut to allow for delivery via the narrow and winding roads. As well, the house incorporates site-built stone walls as particularly strong elements that root the house in its location.
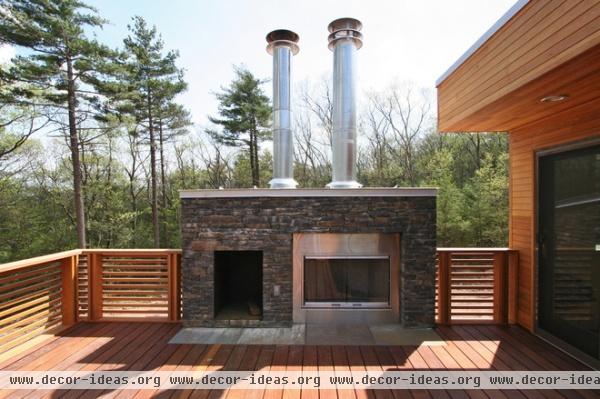
Stone is also found in the hearth, which extends to the rooftop terrace.
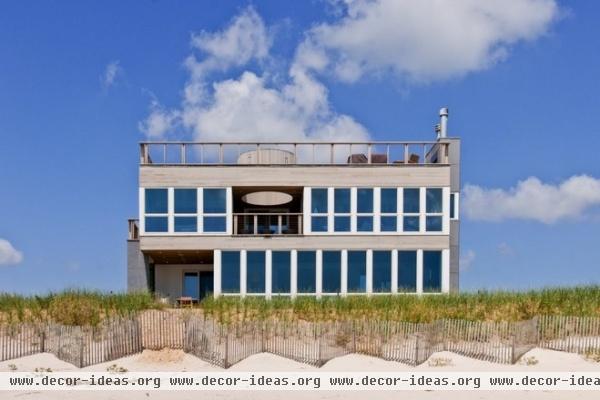
Dune Road Beach House
East Quogue, New York
2012
The last house in this ideabook is the last one in the book, a house at the east end of Long Island. A Two-Story Double-Wide, it is small and compact for the area, where houses are "rural fortresses," in the words of RES:4. Expansive windows open the house to beach and water views, but I'm drawn to the oculus above the second-floor terrace.
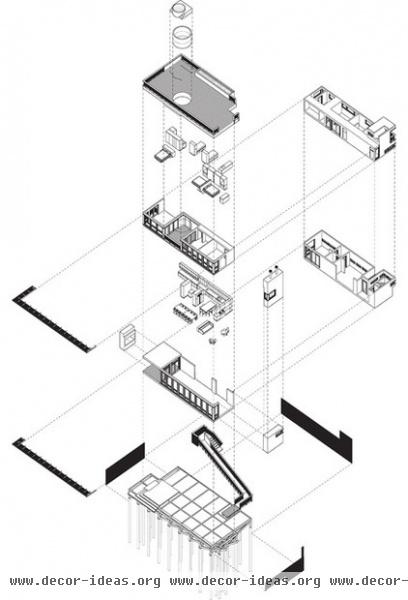
The circular opening can be seen at the top in the house's exploded axon, inserted into a large roof deck.
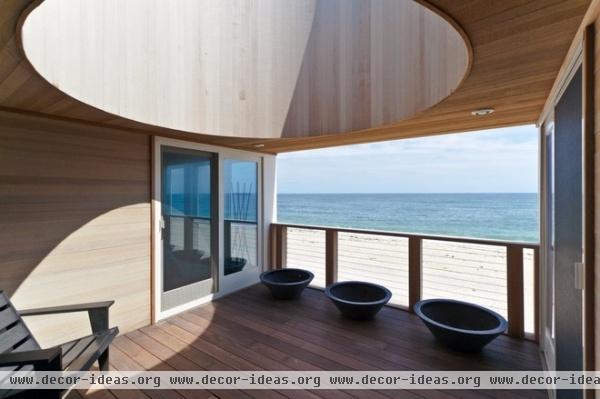
With this oculus Tanney and Luntz have further refined their prefab system to create surprises within the modern modular framework. It's safe to say more surprises will follow in the future as they continue to refine their prefab modern houses.
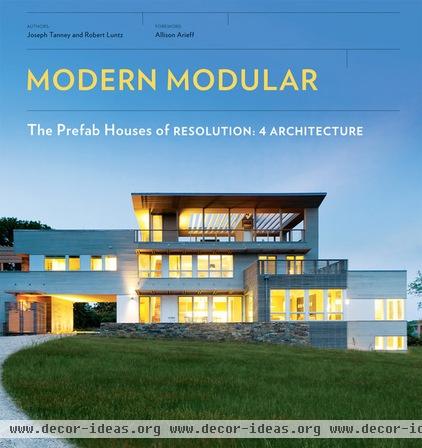
Modern Modular: The Prefab Houses of Resolution: 4 Architecture is available from Princeton Architectural Press.
Related Articles Recommended